choix des réacteurs d'ozonation
Temps de lecture :On a déjà vu à la section sur les oxydants et désinfectants, que l’ozone peut réagir par voie moléculaire (l’oxydant actif est l’ozone) et/ou par voie radicalaire (l’oxydant actif est le radical hydroxyle issu de la décomposition de l’ozone) selon la composition du milieu dans lequel il est transféré. Cette réaction peut modifier le transfert de l’ozone.
aspect cinétique – hydraulique du réacteur
Le choix du réacteur le mieux adapté pour réaliser l’oxydation dépend du régime réactionnel. En général, la vitesse de réaction de l’ozone avec les composés minéraux, organiques et les micro-organismes est formalisée par une équation du deuxième ordre avec des ordres partiels de 1 pour chacun des réactifs :


où : k est la constante de vitesse de la réaction, í est le coefficient stoechiométrique, [M] ([O3]) est la concentration du composé M (de l’ozone dissous), et rM (rO3) est la vitesse de disparition du composé M (la vitesse de consommation de l’ozone dissous). Les valeurs des constantes de vitesse k varient dans de larges proportions selon la réactivité des composés M vis-à-vis de l’ozone. Des indications qualitatives sont données à la section sur les oxydants et désinfectants.
Vu l’ordre partiel 1, un réacteur avec écoulement de la phase liquide piston sera toujours plus performant qu’un réacteur parfaitement mélangé. On s’attachera donc à concevoir les réacteurs d’ozonation de telle sorte que le comportement de la phase liquide soit aussi proche que possible de l’écoulement piston.
cirtères de choix des réacteurs d’ozonation
La valeur du critère de Hatta (Ha), nombre adimensionnel, permet de caractériser le régime de fonctionnement de la réaction d’oxydation et ainsi de diriger le choix du réacteur gaz – liquide selon la caractéristique déterminante comme indiqué au tableau 8. Par exemple :
- un nombre de Hatta très faible signifie que la capacité de transfert du film liquide est grande devant la vitesse de consommation d’ozone : c’est le régime chimique ;
- à l’inverse, lorsque Ha est élevé, la vitesse de consommation d’ozone pourrait être largement supérieure au flux d’ozone transféré : c’est le régime diffusionnel.
Pour une réaction irréversible d’ordre 2, ce critère vaut :

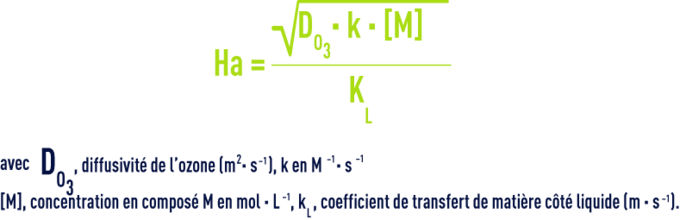
L’expression du flux d’ozone transféré de l’équation (1) devient :


où E représente le facteur d’accélération du transfert dû à la réaction en phase liquide, lequel est lié au nombre de Hatta.

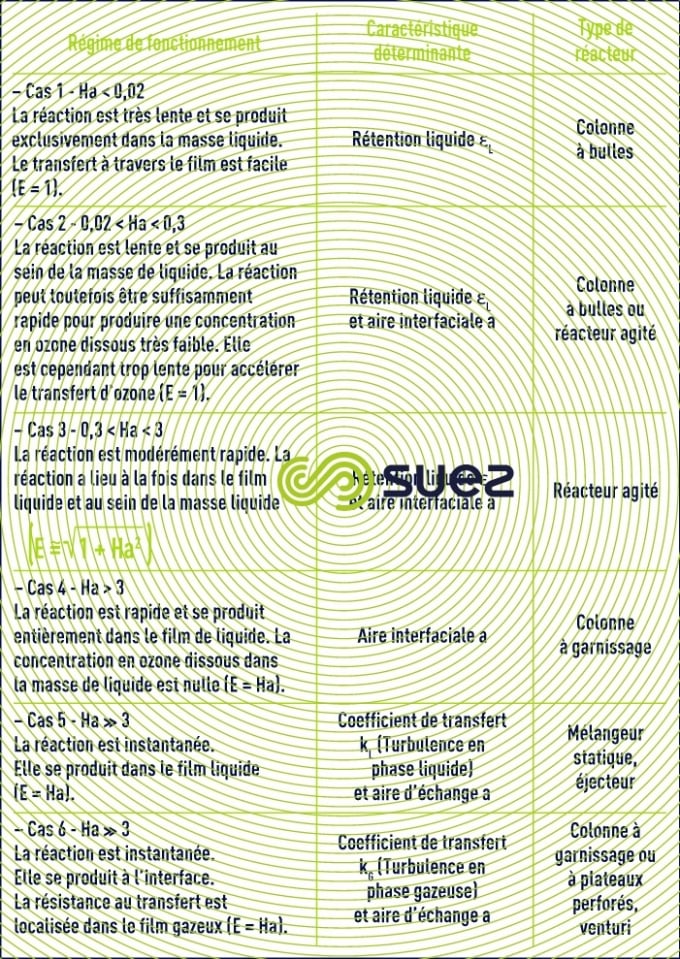

La figure 15 représente les profils de concentration au voisinage de l’interface pour les différents cas explicités au tableau 8 sur la base du modèle à double film.

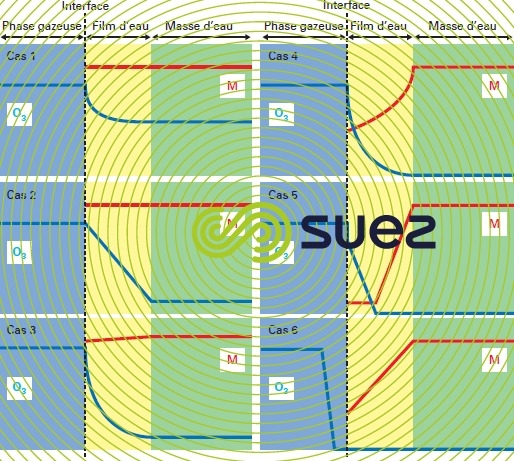

les réacteurs d’ozonation
Les principaux contacteurs ozone-eau sont présentés ci-après selon le classement du tableau 8.
colonne à bulles et chambre d’ozonation équipées de diffuseurs poreux
La colonne à bulles correspond au contacteur le plus classique pour l’ozonation en traitement d’eau. Ce type de réacteur se décline en deux formes, colonne à bulles conventionnelle et chambre d’ozonation à plusieurs compartiments en série. Ces réacteurs sont schématisés à la figure 16. Dans ces réacteurs, les bulles de gaz d’environ 3 mm sont créées par les diffuseurs poreux positionnés à la base du réacteur pour distribuer le gaz sur toute la section de la colonne (photo 10). Les fluides circulent à contre-courant par admission de l’eau en tête de la colonne ou grâce à l’aménagement de cloisons dans chaque compartiment de la chambre d’ozonation. Dans ce type de réacteur, la hauteur d’eau est comprise entre 5 et 7 m au-dessus des diffuseurs. On ajuste le nombre de compartiment (généralement 2 ou 3) en fonction de la vitesse de réaction chimique avec répartition du débit de gaz ozoné suivant l’avancement de la réaction (voir aussi figure 26).

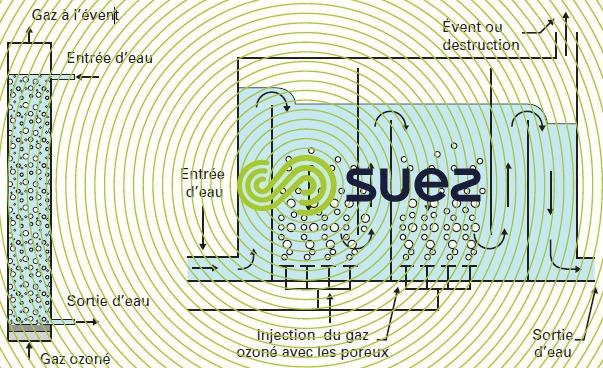


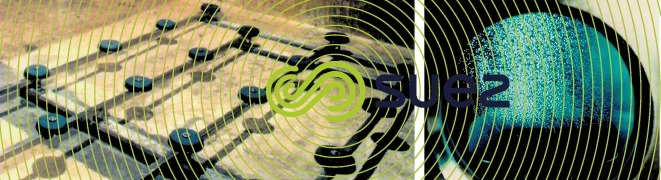

réacteur équipé de turbine ou de diffuseur radial
Ce type de réacteur agité permet d’homogénéiser le mélange dans la zone de contact en créant une dispersion du gaz dans toute la masse liquide.
Ce mélange peut être réalisé grâce à :
- une turbine avec pales radiales qui aspire l’eau à traiter et la refoule à proximité du flux de gaz ozoné tout en cisaillant les bulles de gaz (figure 17) ;
- un diffuseur radial qui éjecte un jet turbulent gaz ozoné – eau créée par un hydroéjecteur (figure 18). Dans ce dernier, le gaz est aspiré, entraîné et dispersé dans l’eau recirculée au moyen d’une pompe sous l’effet de la dépression créée à la contraction de la veine liquide. Cette seconde variante assure un meilleur transfert de l’ozone : réalisation simultanée de la dispersion du gaz et du mélange avec l’eau à traiter dans l’hydroéjecteur.

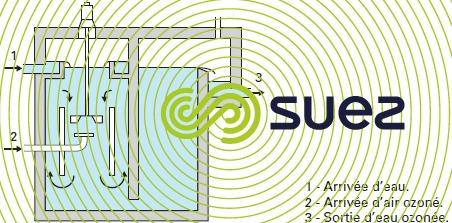


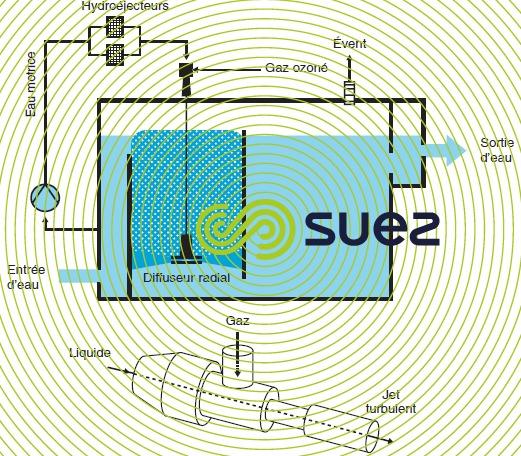

tube en U
Le tube en U comprend deux tubes concentriques verticaux qui communiquent en partie basse (figure 19). Le gaz ozoné est entraîné et dispersé dans l’eau à traiter injectée par une pompe à forte vitesse (1,7 m · s–1 environ) en flux descendant dans le tube central. Le rapport maximum admissible des débits de gaz et de liquide s’élève à 0,17. Dans le tube central, la vitesse d’eau et l’augmentation de la pression produisent des bulles de petite taille. L’émulsion créée remonte ensuite dans la partie annulaire. La pression hydrostatique et le temps de séjour des bulles de gaz sont importants du fait de la hauteur d’eau de l’ordre de 20 m. Le transfert d’ozone est ainsi favorisé.

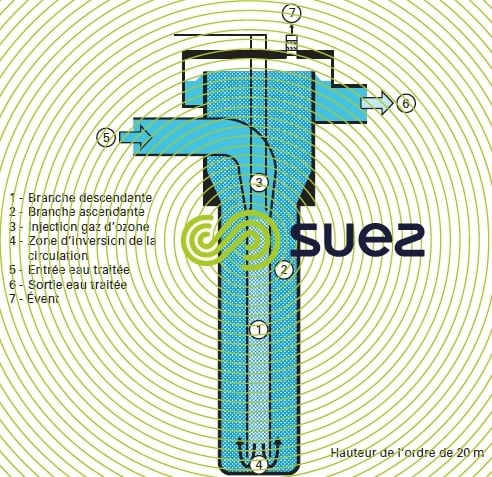

colonne à garnissage
Dans ce type de réacteur, l’eau à traiter est pulvérisée à contre-courant du gaz ozoné (figure 20). Le garnissage contenu dans le corps du réacteur a pour rôle de répartir la phase liquide sous forme de film et de gouttelettes tout au long de son écoulement gravitaire. Le mouillage des éléments du garnissage développe la surface d’échange gaz-liquide.
Le garnissage peut être disposé en vrac ou structuré. Il peut être fabriqué en acier inoxydable ou en céramique. Il doit offrir une surface par unité de volume la plus élevée possible et par une perte de charge faible.

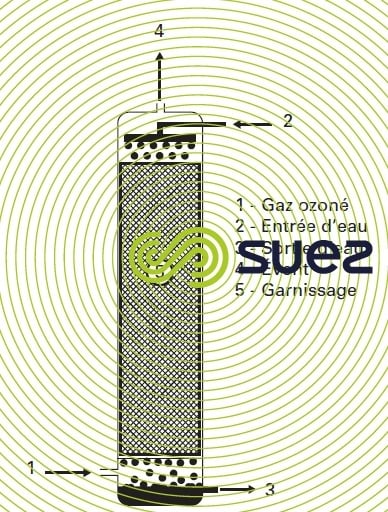

mélangeur statique
Un mélangeur statique est constitué d’un tube dans lequel sont montés des éléments fixes qui permettent le mélange des phases par divisions successives du flux. Le mélangeur statique est monté en conduite ; l’eau circule au travers à une vitesse de 0,5 à 1,7 m· s–1 grâce à une pompe et l’ozone est injecté en amont de l’écoulement par des buselures. Le mélangeur statique génère des bulles de l’ordre du mm qui créent une aire interfaciale très élevée. La caractéristique essentielle des mélangeurs statiques est la perte de charge qui détermine la puissance dissipée et fixe ainsi la taille des bulles.
Cette dernière varie en fonction des débits des fluides, du type et du nombre des éléments du mélangeur. Elle peut varier de 0,05 à 0,3 bar par mètre de longueur du mélangeur statique. Ce type de dispositif est utilisé pour l’injection du gaz en tête de contacteur au même titre que l’hydroéjecteur mais aussi pour transférer l’ozone en phase liquide. Un schéma classique d’installation comprend un premier mélangeur statique en dérivation pour la dispersion du gaz et un mélangeur statique principal pour le transfert d’ozone (figure 21). Selon la perte de charge admissible, le mélangeur statique secondaire est remplacé par un hydroéjecteur. L’installation nécessite généralement une colonne de dégazage en aval pour la séparation des phases.

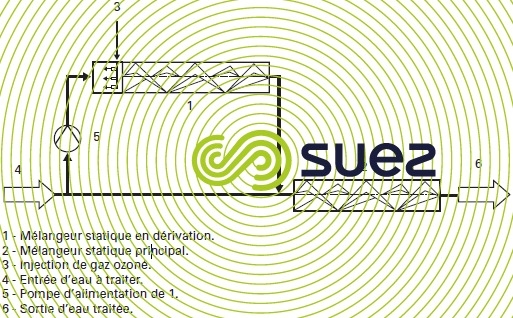

Les critères de performances des principaux réacteurs d’ozonation décrits sont comparés dans le tableau 9.

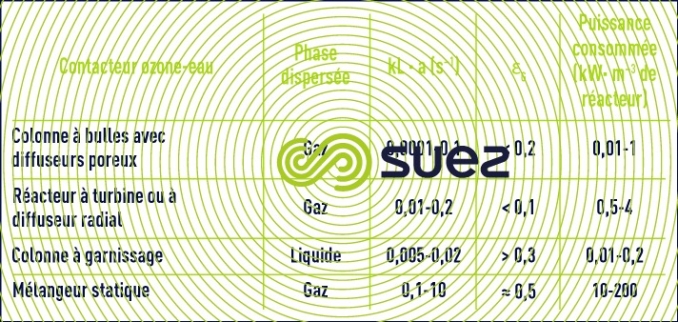

Pour chaque application, le choix du réacteur est dicté par le facteur déterminant du procédé qui est :
- le temps de contact pour les réactions lentes ;
- l’hydrodynamique pour les réactions rapides et moyennement rapides (l’écoulement piston est alors recherché) ;
- le transfert d’ozone pour les réactions très rapides (les contacteurs avec aire interfaciale élevée sont les plus adaptés).
Le tableau 10 récapitule les avantages et inconvénients techniques liés à chaque réacteur et introduit le domaine d’application qui leur correspond.

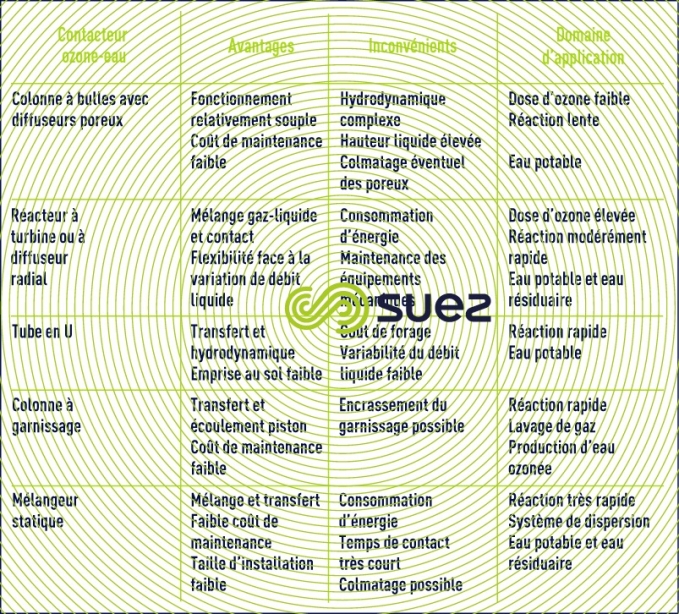

Outil Marque-page
Cliquez sur l'outil marque-page, puis surlignez le dernier paragraphe lu pour pouvoir poursuivre ultérieurement votre lecture.
