industrie des métaux
Temps de lecture :extraction minière
Les questions liées à la gestion de l’eau dans le secteur minier varient d'un site à l’autre et doivent être traitées localement. L'eau est principalement utilisée pour le traitement des minerais et la récupération des métaux, mais aussi pour le contrôle de la poussière et permet également de répondre aux besoins des travailleurs sur le site. La quantité d’eau requise par une mine dépend de l'emplacement (géologie, climat), de la durée de vie de la mine, de la taille de celle-ci et du type de minerai extrait ainsi que du processus d'extraction utilisé. Les effluents peuvent être acides ou alcalins, et peuvent contenir des métaux dissous et des complexes organométalliques générés par le traitement des minéraux, ou se produisant naturellement avec des substances organiques telles que des acides humiques à longue chaîne et les acides carboxyliques d'opérations minières.
Les risques environnementaux dans l'exploitation minière sont de plus en plus pris en compte. Par exemple, le «drainage rocheux acide» ou ARD généralement associé au minerai sulfuré (tels que Pb, Zn, Cu, Au, et d'autres minéraux) qui réagit au contact de l’oxygène et de l’eau pour produire des effluents acides, chargés en métaux et sulfates, est un problème auquel l’industrie minière doit faire face dans la durée et parfois bien au-delà de la période d’exploitation du gisement.

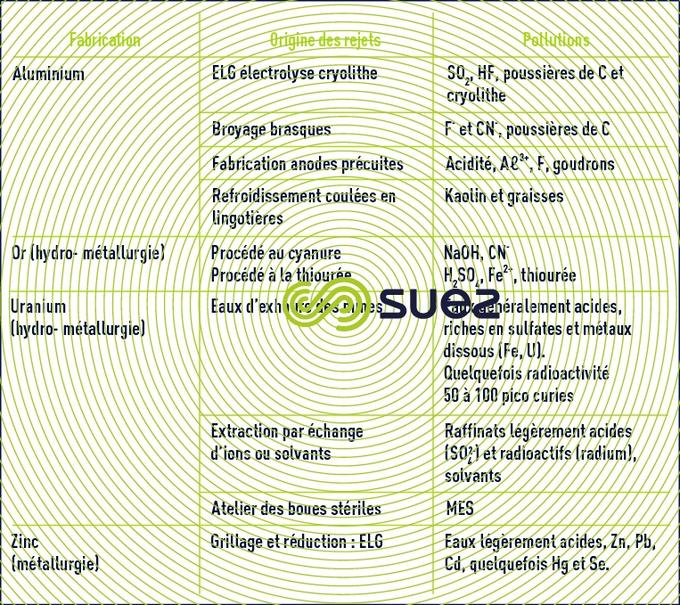

sidérurgie
L’industrie sidérurgique regroupe les ateliers de fabrication de fonte et d’acier à partir de minerais.
Une usine sidérurgique intégrée, comprend plusieurs unités :
- agglomération : préparation du minerai et des charges des hauts fourneaux qui serviront à faire la fonte (pratiquement pas d’effluents) ;
- cokerie : à partir de charbon, fabrication du coke sidérurgique qui sert dans les hauts fourneaux à la réduction du minerai ;
- hauts fourneaux : élaboration de la fonte à partir du coke et des minerai de fer ;
- aciérie : à partir de la fonte, élaboration des aciers liquides de toutes nuances (fonction des charges ajoutées) ;
- aciérie électrique : élaboration d’acier particulier et recyclage de ferrailles ;
- coulée continue : à partir de l’acier liquide, formation des brames, blooms, billettes qui serviront à l’élaboration des produits finis ;
- laminage à chaud : les produits issus de la coulée continu sont réchauffés et laminés pour devenir des tôles, poutrelles, fils… ;
On peut distinguer 4 groupes de rejet sur une usine sidérurgique intégrée .
cokéfaction
Elle génère des eaux ammoniacales qui proviennent de l’humidité du charbon (8 à 15%) et d’eau de formation (3 à 5 %) générée lors de la décomposition thermique du charbon.
Ce sont les eaux ammoniacales faibles, riches en phénols. Le lavage du gaz génère lui-même les eaux ammoniacales fortes, riches en NH4 libre.

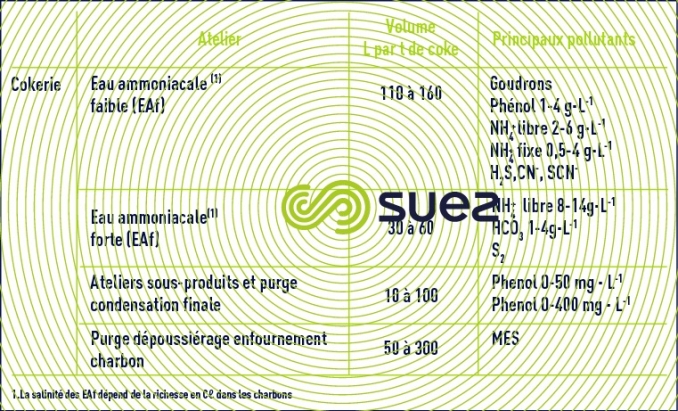

lavage de gaz
Il concerne les ateliers de l’agglomération, les hauts fourneaux, (et la réduction directe) et les aciéries. Dans la presque totalité des usines, les circuits sont semi-ouverts et seules de faibles purges sont à traiter. La pollution qui doit être traitée pour le recyclage est principalement constituée par les matières en suspension. Les purges peuvent subir des traitements plus complexes pour mise en conformité avant rejet.
laminage
Depuis la coulée continue de l’acier et l’écriquage des brames, jusqu’à l’élaboration des produits (trains à bande, trains à profilés, trains quarto, trains à fil, laminoirs à tubes) l’eau intervient dans toute une série d’opérations mécaniques, décalaminage, refroidissement des machines (rouleaux) et du métal par aspersion. Elle entraîne des oxydes (battitures) auxquels peuvent s’ajouter des petites quantités de polluants (hydrocarbures, graisses, fluorures) provenant de la lubrification des cages ou de l’acier. La présence d’une pollution dissoute est exceptionnelle (fuites de fluide hydraulique de coulée continue ou de laminage). Tous ces circuits peuvent donc être semi-ouverts avec une faible purge de déconcentration à traiter.
purge de circuits de refroidissement
Certains circuits de refroidissement sont sans contact direct avec le produit à refroidir (gaz ou métal). Ces circuits peuvent être dans ce cas gérés comme des circuits de refroidissement classiques de type semi ouverts avec une purge nécessaire au maintien de salinité dans la boucle. Néanmoins, l’environnement atmosphérique pouvant être parfois très poussiereux, il faudra une vigilance accrue sur la gestion des matières en suspension.
Au total, les eaux d’appoint d’un complexe sidérurgique bien équipé en recyclage peuvent représenter 3 à 6 m3 d’eau par tonne d’acier, compte tenu d’un facteur global de concentration de 3 à 4 et le volume total des effluents des circuits semi-ouverts est alors de 1 à 1,5 m3·t–1 acier (tableau 66).

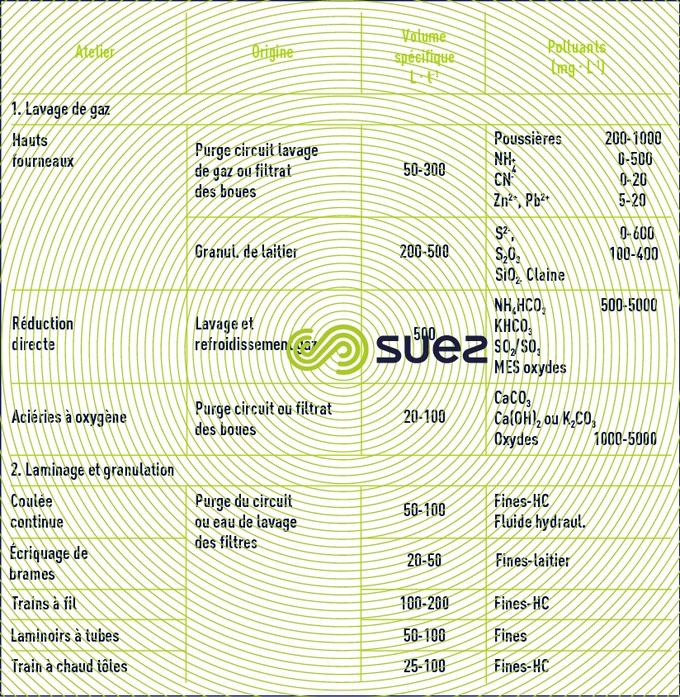

industries des traitements de surface
origine et nature des rejets
Le traitement de surface met en œuvre :
- le décapage : il produit des eaux de rinçage très chargées en Fe2+ et en H2SO4 s’il est sulfurique. S’il est chlorhydrique, et c’est devenu le cas le plus général, la régénération thermique de HCℓ peut supprimer une grande partie des rejet d’acidité et de fer dissous.
- le laminage
- le dégraissage et recuit
- la déposition par voie chimique (étamage ; electrozingage, galvanization,..)
Chacune de ces opérations doit elle-même être suivie de rinçage courant.
L’ensemble des effluents doit être séparé en trois catégories :
- bains usés concentrés ;
- eaux de lavage moyennement concentrées en produits susceptibles de précipiter (savons, graisses, sels métalliques) ;
- eaux de rinçage diluées et éventuellement recyclables après traitement.

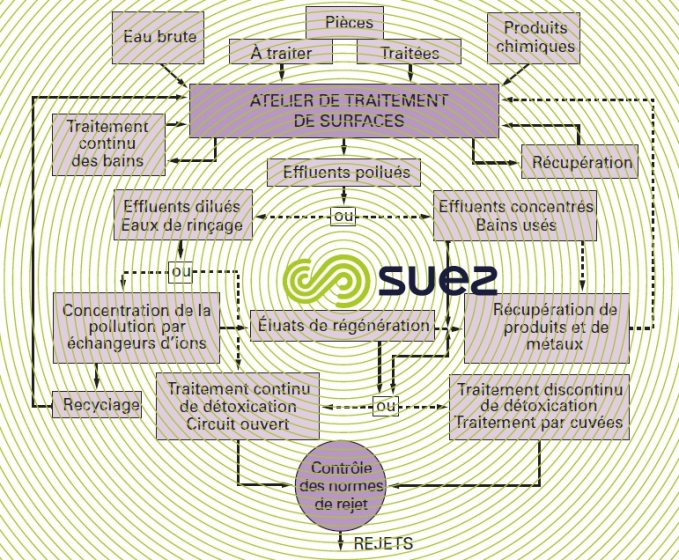

Tant pour la sécurité que pour faciliter le traitement, on doit séparer les effluents acides et chromatés des effluents alcalins et cyanurés.

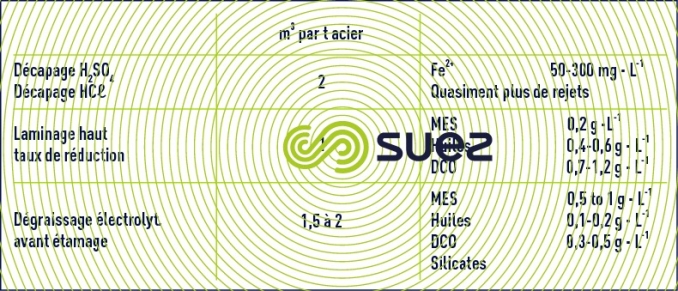

classification des polluants
La pollution se répartit en plusieurs familles :
- polluants toxiques tels que CN–, Cr(VI), F– ;
- polluants provoquant une modification du pH (acides ou bases) ;
- polluants dont la présence augmente la teneur en MES, comme les hydroxydes, les carbonates et les phosphates ;
- polluants qui font l’objet d’une réglementation particulière, S2–, Fe2+ .
- polluants organiques (EDTA…), provenant en particulier du dégraissage.
Tous les composants des bains se retrouvent dans les eaux de rinçage, qui peuvent également contenir des ions métalliques provenant de l’attaque des pièces traitées.
prévention
Elle a pour but de diminuer les émissions de polluants au niveau de l’atelier par :
- diminution des entraînements (géométrie des montages, accrochage des pièces, amélioration des temps d’égouttage) ;
- modification des caractéristiques des bains.
récupération de l’eau
La rationalisation de l’utilisation de l’eau dans les ateliers est primordiale. Pour un travail donné et à qualité de rinçage et de fabrication égales, des structures de rinçage permettent des économies importantes par :
- des rinçages statiques ou de récupération ;
- des rinçages en cascade, éventuellement recyclables sur échangeurs d’ions.
récupération des matières premières
Leur récupération « in situ » est possible par :
- échange d’ions (sels de chrome, acide des bains de décapage…) ;
- électrolyse (Cu, Zn, Cd, Ag, Ni…).
Cette dernière voie est la meilleure sur les plans de l’économie et de l’environnement.
Un traitement de concentration sur osmose inverse peut être intéressant, soit avant électrolyse, soit pour « remonter » les bains.
Outil Marque-page
Cliquez sur l'outil marque-page, puis surlignez le dernier paragraphe lu pour pouvoir poursuivre ultérieurement votre lecture.
