autres références
Temps de lecture :Georgia Pacific
Georgia Pacific est situé à Arrabloy (45) la production principale est la production de ouate de cellulose. L’établissement est classé au titre des ICPE et possède un arrêté de classement réglementant entre autres ses rejets liquides industriels.
Avant rejet en Loire, pour respecter son arrêté d’exploitation, Georgia Pacific disposait d’une filière de traitement constituée de flottateurs à air dissous et de deux lagunes de décantation ; afin de minimiser son impact sur le rejet et obtenir des flux conforment aux nouvelles directives papetière notamment sur les ratios de DCO rejetée par rapport aux tonnes de papier produit, Georgia Pacific a décidé la construction d’une nouvelle station de traitement.
données de base
Les données suivantes ont servi de base de dimensionnement à notre offre.

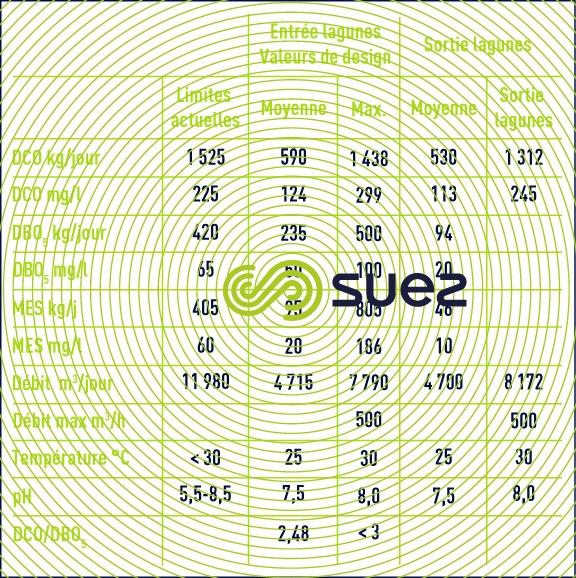

Garanties demandées pour le rejet dans la Loire :

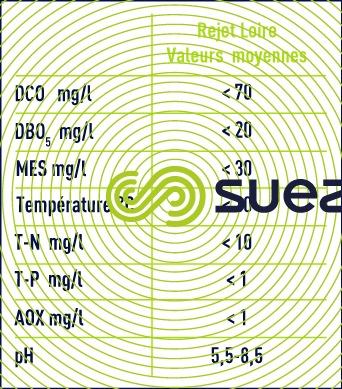

la filière de traitement des effluents
- Bassin tampon en génie civil, d’une capacité utile de 1850 m3. Ce volume permet d’admettre une pointe de 500 m3/h durant 6 h maxi, une fois par semaine. Le débit de traitement (débit de reprise) est fixé à 300 m3/h. Ce bassin est équipé d’un agitateur submersible ou en option d’un aérateur type Tsurumi. Cette aération serait asservie au potentiel d’oxydoréduction, afin de limiter l’activité biologique dans ce bassin.
- Traitement biologique sur cultures mixtes, constitué de deux bassins METEOR® C en génie civil, constituant deux étages de traitement en série. Ils pourront être chargés à 30/50% de supports de Météor C. L’un ou l’autre de ces bassins pourra être by-passer en cas d’opérations de maintenance.
- Ces bassins sont équipés d’un réseau d’air en acier inoxydable avec Vibrairs et d’une grille de sortie en acier inoxydable. Les réseaux d’air sont alimentés par trois surpresseurs d’air insonorisés (dont un en secours commun).
- Clarification des effluents par flottation avec conditionnement chimique préalable constitué de :
- Un bassin de coagulation en génie civil, équipé d’un agitateur pendulaire.
- Un bassin de floculation en génie civil.
- Un flottateur en génie civil, équipé d’un ensemble de raclage.
- Un ensemble de pressurisation pour le flottateur comprenant un ballon de pressurisation et deux pompes horizontales (une en secours).
- Un bassin de récupération des boues flottées en génie civil,équipé d’un agitateur pendulaire, d’une pompe de reprise des boues et d’une pompe de recyclage des boues vers les bassins Météor.
- Une colonne pour recyclage éventuel de l’eau clarifiée.
- Un ensemble de contrôle final des effluents traités,avant rejet vers les lagunes existantes.
- Ensemble de postes de dosage, nécessaire à la mise en œuvre du traitement constitué de :
- Une cuve de coagulant (sulfate d’alumine), équipée de pompes doseuses.
- Une cuve d’acide phosphorique, équipée de pompes doseuses.
- Un poste de préparation automatique de floculant en poudre, équipé de pompes de dosage.
- Fosse de reprise toutes eaux
La filière de traitement des boues biologiques est composée des éléments suivants :
- Une cuve de stockage des boues en PEHD, d’une capacité de 30 m3, équipée d’un agitateur pendulaire et d’une pompe de reprise.
- Déshydratation des boues par centrifugation avec une décanteuse centrifuge type D2L insonorisée, complétée d’un poste de préparation automatique et de dosage de floculant en émulsion.
- Une pompe gaveuse de reprise des boues déshydratées vers une benne à boues placée dans un local dédié.
- Unité de désodorisation sur caisson de charbon actif, pour le traitement du stockage des boues, du local benne à boues et du local centrifugation.
schéma du process retenu

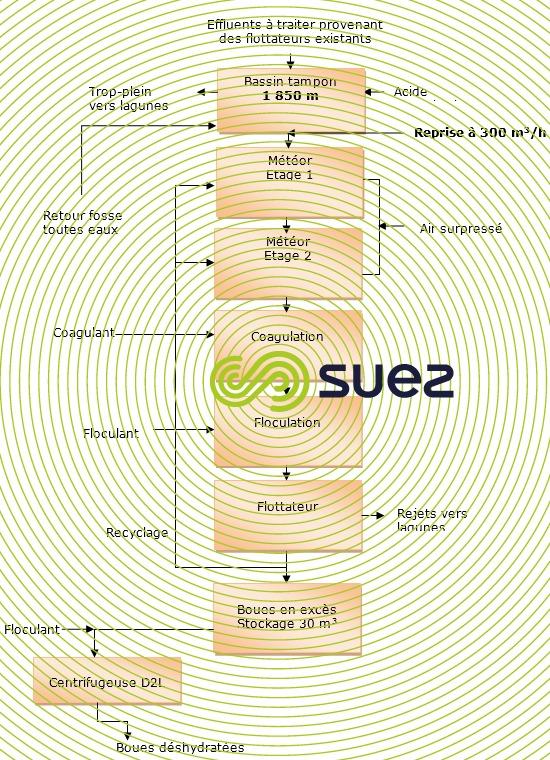


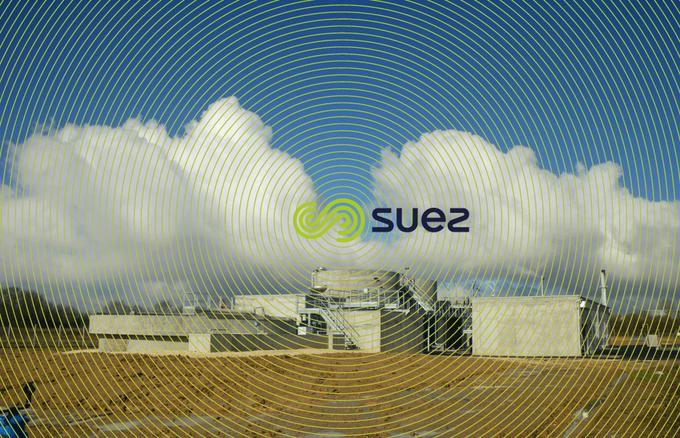


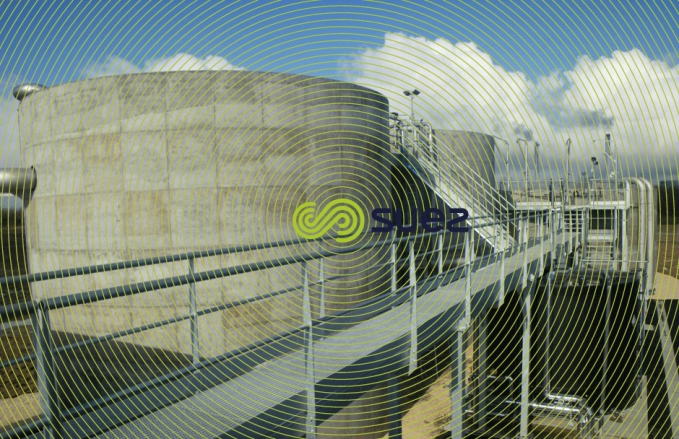

papeteries du Léman
Les Papeteries du Léman (PDL) font partie du groupe Bolloré Paper Division qui est leader mondial dans la production de papiers fins et spéciaux .
La fabrication de papiers fins représente une production d'environ 60 000 tonnes/an.
La pâte à papier spéciale est fabriquée sur le site à partir de lin et de chanvre. Les principaux produits fabriqués à PDL sont les papiers à cigarettes, les papiers cosmétiques, les papiers dédiés à l'impression numérique, les papiers minces opaques destinés à la communication, l'édition et l'impression.
C’est en 2004, que PDL a construit sa propre station d’épuration sur son site de fabrication de papiers spéciaux afin d’arrêter le traitement à la STEP de Thonon.
la fabrication de pâte à papier génère différents types d'effluents.
Les eaux de défilage qui proviennent du défilage du lin et du chanvre :
- La liqueur noire issue de la cuisson du lin et du chanvre
- Les eaux de blanchiment qui résultent du blanchiment de la pâte à papier
- Les sauces de couchage qui proviennent du lissage du papier
- Les eaux blanches issues de la fabrication du papier
Ces cinq effluents ont des caractéristiques différentes ; la nature de la pollution qu’ils contiennent peut être organique, minérale, carbonée, azotée ou bien phosphorée.
La taille et la forme des particules contenues dans ces effluents divergent aussi ; il peut s’agir de pollution soluble, ou de pollution insoluble : particules colloïdales ou matières en suspension...). Pour ces raisons, ces cinq effluents sont prétraités différemment en amont puis se rejoignent en un même traitement final biologique.
la station d’épuration traite l’ensemble de ces eaux usées

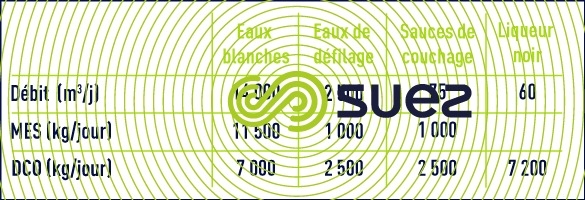

les principales normes de rejet



description de l’installation
Dans le but d’améliorer son bilan environnemental, PDL a initialement mandaté la société Granit technologies pour installer son procédé de précipitation de la lignine (LPS) contenue dans les liqueurs noires. L’unité LPS (Lignine Precipitation System) est une installation de précipitation acide de la lignine contenue dans les effluents de cuisson de pâte. Le LPS permet la réduction d’environ 35 % de la teneur en matières organiques de la liqueur noire, et en élimine principalement la fraction non biodégradable qui est la lignine. L’effluent obtenu en sortie du LPS est nommé filtrat.
Le filtrat obtenu via l’unité LPS est traité par oxydation par voie humide (OVH). Le procédé d’oxydation par voie humide (OVH) est utilisé pour le traitement d’effluents fortement chargés en matières organiques.
L’installation OVH réalisée a été la première référence industrielle en France d’un procédé d’oxydation par voie humide.
L’OVH utilise de l’oxygène ou de l’air sous pression (150/180 bars environ) à température élevée (200 à 300°C) pour détruire par oxydation les matières organiques contenues dans l’effluent.
Les matières organiques sont oxydées en eau et en dioxyde de carbone dans un réacteur pressurisé.
La réaction a lieu dans cinq réacteurs tubulaires.
Comme l’oxydation de composés organiques est exothermique, la réaction est auto-entretenue si la concentration en matière organique est suffisante ce qui permet dans des conditions optimales de récupérer de l’énergie sous forme de vapeur. Aucun gaz nocif n’est généré par le traitement, aucune boue n’est produite.
La réaction produit un effluent traité compatible avec un traitement biologique. L’objectif de ce traitement est l’élimination de 75 à 90% de la matière organique contenue dans les liqueurs, en vue d’être compatible pour un traitement biologique de finition.
description de l’installation de traitement des eaux

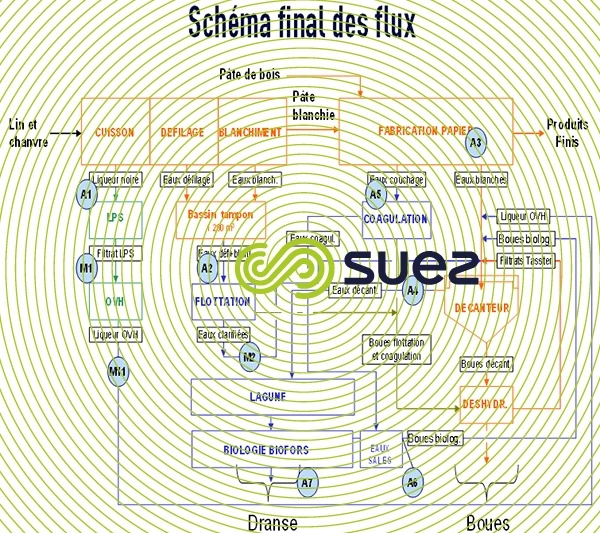

le dégrilleur
Les eaux issues de la fabrication du papier sont chargées de fibres végétales. Il faut donc séparer de l’effluent, les matières solides ou particulaires volumineuses, susceptibles de gêner les étapes ultérieures de traitement ou d’endommager les équipements.
Cette grille va retenir les matières solides volumineuses de plus de 5 cm.
le clarifloculateur/décanteur
Après injection d’un floculant dans les eaux de la machine à papier, l’effluent à traiter est envoyé dans le clarifloculateur. Ce traitement primaire a pour but de retenir le maximum de matières en suspension présentes dans les eaux usées.
Le clarifloculateur permet d’éliminer 85 % de la partie décantable des matières solides en suspension. Il permet également un abattement de 35 à 50 % de la DCO et DBO5.
coagulation/floculation/décantation
Les eaux de couchage présentent une teneur élevée en charges minérales ainsi qu’en matières organiques. Ces eaux contiennent également des composées comme le latex et PVA (alcool polyvinylique) utilisés durant cette étape de fabrication.
Ces composés sont éliminés par une étape de coagulation/ floculation/décantation.
Le surnageant est ensuite mélangé aux eaux de défilage et dirigé dans l'unité de flottation pour un affinage du traitement.
Les boues soutirées du décanteur, sont envoyées dans le stockage de boues avant la déshydratation.
coagulation/floculation/flottation
Les eaux de défilage comme leur nom l’indique, contiennent de la filasse provenant du défilage du lin et du chanvre qui servent à la fabrication de la pâte à papier. Les eaux de défilage sont traitées par coagulation/ floculation/flottation.
les biofiltres
Les biofiltres constituent le traitement biologique final de tous les flux préalablement prétraités, c'est-à-dire : l’effluent provenant de l’unité OVH, les eaux de défilage et de blanchiment, les eaux de couchage et les eaux de la machine à papier.
traitement des boues
Les boues soutirées sont stockées dans le stockeur de boues. Ce stockeur permet de gérer les flux de boues qui entrent dans le trommel pour y être déshydratées.
Les boues issues du traitement des effluents des Papeteries du Léman sont valorisables car en amont les produits difficiles, non biodégradables tels que la lignine ont été éliminés.
Les boues deshydratées ont une siccité d’environ 50 %.
Elles présentent un intérêt agronomique en raison de leur teneur en matière organique. Les boues de la STEP sont donc valorisées via l’épandage agricole, ou bien sont envoyées en briqueterie.

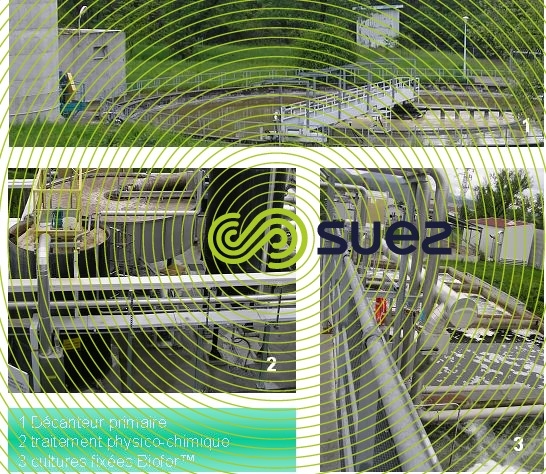


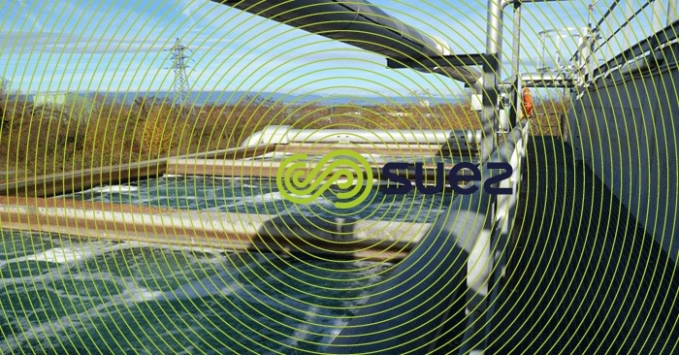

papeterie de Delicarta (Porcari, Italie), usine de réutilisation des eaux usées
La station de réutilisation des eaux usées traite les effluents résiduaires de la papeterie de Delicarta produisant 120 000 tonnes de papier par an. La papeterie peut produire tous les principaux types de papier-tissu : papier toilette, papier absorbant, serviettes de tables et mouchoirs.
La station est située en Toscane (Italie), dans une zone regroupant plusieurs papeteries. Du fait de la forte concentration d’activités industrielles dans la zone, et après plusieurs dizaines d’années d’exploitation des ressources en eau, il est devenu urgent de réduire la pression sur l’environnement en limitant les prélèvements d’eau souterraine. Il a donc été proposé d’installer une station de réutilisation capable de collecter et réutiliser les effluents résiduaires.
La station existante a été conçue pour récupérer une partie de la cellulose contenue dans les effluents résiduaires. Elle comprend :
- Un système de dégrillage vertical destiné à éliminer les résidus les plus grossiers (trois appareils, un par ligne de production)
- Un système de flottation à air dissous (DAF) destiné à récupérer la cellulose (trois appareils, un par ligne de production) ;
- Un décanteur en béton commun destiné à l’élimination des MES ;
- Un bassin d’égalisation commun.
La nouvelle station de réutilisation a donc été conçue pour traiter les eaux du bassin d’égalisation, qui étaient auparavant envoyées vers la STEP municipale.
La nouvelle station de réutilisation comprend un bioréacteur à membranes (MBR) ainsi qu’une unité de traitement par osmose inverse ( OI ). La saumure issue du procédé d’OI est envoyée à la STEP municipale. Le processus de traitement globalement utilisé pour les eaux résiduaires issues des procédés de production est présenté de manière détaillée en Figure 23. La Photo 15, quant à elle, explique le traitement par MBR qui est appliqué.

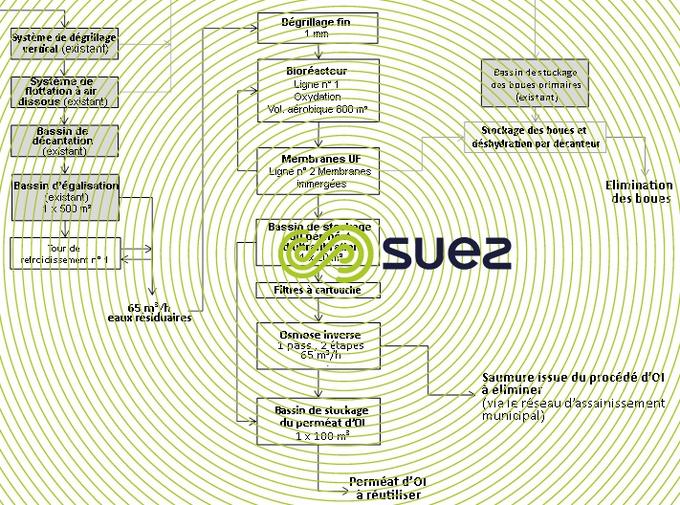


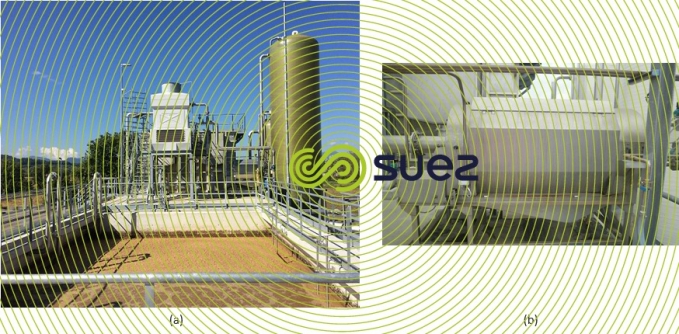

Comme indiqué en figure 23 et en photo 15, la station de réutilisation a été équipée d’un tamis à tambour (trous d’1 mm) et d’une tour de refroidissement, afin de protéger le procédé MBR grâce à un traitement supplémentaire. Le traitement biologique intervient alors, au moyen d’un réacteur aérobie à boues activées, dont la fonction principale est d’éliminer la pollution organique ( DCO ). Les excédents de boues biologiques sont envoyés vers le bassin de stockage des boues, où les boues biologiques et les boues primaires sont mélangées puis acheminées vers un décanteur pour déshydratation.
De plus amples informations sur le fonctionnement du bioréacteur à membranes figurent dans le Tableau 17. Les conditions d’exploitation ont été définies sur la base d'une exploitation de 9 mois.

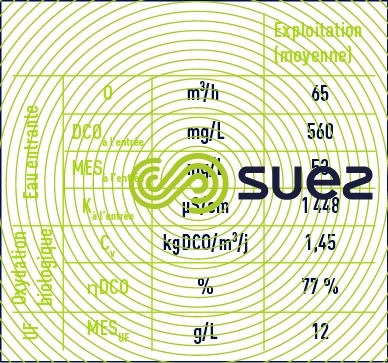

Le système d’ultrafiltration fonctionne conformément aux indications de conception. Les opérations de nettoyage chimique sont réalisées au moyen d’hypochlorite de sodium et d’acide citrique. Les nettoyages d’entretien sont réalisés une fois par semaine et les nettoyages de récupération une fois par an.
Les eaux traitées par ultrafiltration sont ensuite envoyées vers le bassin de stockage du perméat d'ultrafiltration. Une partie du perméat d’ultrafiltration est extraite et envoyée vers l'unité de traitement par OI, tandis qu’une autre partie contourne l’unité de traitement par OI pour être mélangée au perméat d’OI. Le débit du perméat à l’entrée de l’unité d’OI et celui du perméat contourné sont régulés en fonction des besoins de traitement de la papeterie.
L’unité de traitement par OI (Photo 16) est utilisée selon les besoins en eau réutilisée, comme l’indique le tableau 18. Le pH de l’eau entrante est contrôlé par dosage du HCl afin de réduire l’encrassement et la consommation de produits chimiques.

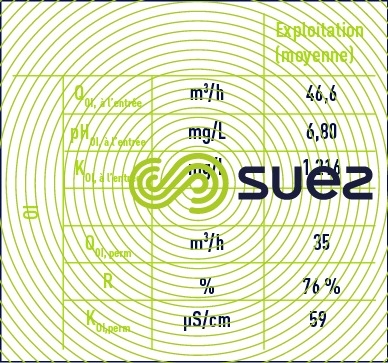


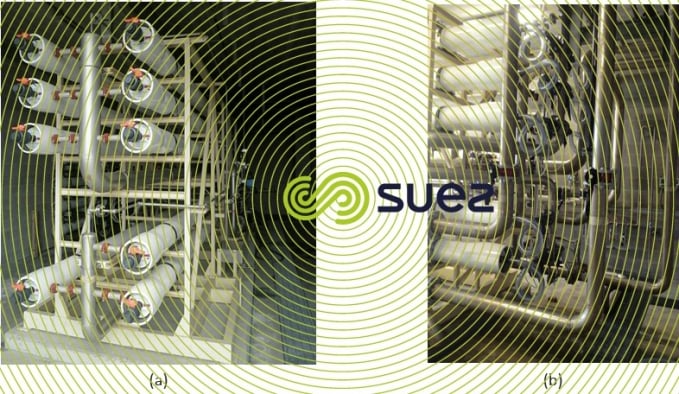

L’installation de la station de réutilisation a eu plusieurs avantages. Grâce à elle, le volume d’eaux souterraines prélevé a été divisé par deux, passant de 700 000 m3/an à 350 000 m3/an. L’impact sur la station d’épuration municipale a également fortement baissé, ce qui a eu pour effet de réduire de manière significative les coûts d’élimination et d’améliorer le réseau d’assainissement de la plaine de Lucca.
De plus, l’approvisionnement en eau de process issue de la station de réutilisation a permis de réduire les coûts liés à l’utilisation de produits chimiques destinés à l’adoucissement de l’eau brute, qui était significative en raison de la dureté de l’eau souterraine dans la plaine de Lucca. Cette étape de la production de papier a gagné en stabilité et le cycle entier de production est devenu plus propre, ce qui a également permis de régler certains problèmes liés à la production de papier, à savoir les dépôts calcaires ou l’encrassement des machines, et même la formation de tâches sur les produits finis.
Bien que peu énergivore, il est indéniable que la station de réutilisation contribue à augmenter la consommation énergétique du site. Toutefois, cette augmentation est inférieure à 3 %, et l’augmentation de la consommation d’électricité est mesurable mais peu significative.
Outil Marque-page
Cliquez sur l'outil marque-page, puis surlignez le dernier paragraphe lu pour pouvoir poursuivre ultérieurement votre lecture.
