la conception d'un atelier de séchage
Temps de lecture :Si le choix de la technologie de séchage est essentiel, la conception globale de l’atelier est également très importante car de la bonne ingénierie des équipements périphériques, dépend la réussite globale de l’atelier.
L’atelier de séchage comprend comme principaux équipements périphériques :
- la manutention des boues humides puis des boues séchées ;
- la boucle du fluide caloporteur ;
- le traitement des buées, avec ou sans récupération de chaleur ;
- le stockage des produits séchés ;
- la ventilation de l’atelier de séchage ;
- optionnel : la mise en forme des produits séchés via la pelletisation ;
- la sécurité globale de l’atelier de séchage (voir la sécurité des ateliers de séchage).
La disponibilité globale d’un atelier de séchage dépend donc de tous ces équipements périphériques, et pas uniquement du sécheur.
Cette conception doit être gérée dans le détail. Dans la suite de ce chapitre, seules les généralités sont abordées.

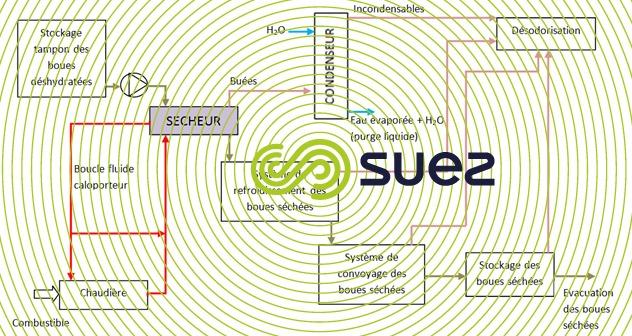

la manutention des boues déshydratées
Il faut préférer le pompage en choisissant avec soin les domaines d’application des pompes à rotor excentré et celui des pompes à piston (Manutention et stockage des boues). Les boues issues de filtre presse doivent être préalablement émottées.
Dans le cas d’atelier de séchage non intégré dans une station d’épuration et traitant des boues d’origines différentes et délivrées sur site après une période de stockage et transport, il est fortement recommandé de faire précéder les accessoires de manutention par un filtre séparateur de corps étrangers et d’organiser les différentes réceptions suivant la siccité et la destination finale des boues.
Il faut noter que le stockage des boues déshydratées change leur rhéologie (flexibilité sur la gestion du flux de boues déshydratées mais exploitation plus difficile du séchage en aval).
le refroidissement des boues séchées
Il est important de refroidir les boues séchées avant leur stockage afin de limiter les risques vis-à-vis de l’auto-échauffement. Certains sécheurs permettent d’obtenir en sortie de sécheur des boues séchées ayant une température suffisamment basse pour être directement stockées (cas de l’Evaporis™ LE), cependant la plupart des sécheurs thermiques nécessitent un système de refroidissement des boues séchées. Le système le plus fréquemment rencontré est la vis de refroidissement.
la manutention des boues séchées
C’est une étape essentielle car bien souvent lors de ces manutentions on dégrade, du moins partiellement, la structure granulée du produit. Elle est aussi source d’abrasion. De surcroît, ce poste doit être protégé par des règles strictes de sécurité (voir la sécurité des ateliers de séchage).
Il existe différents types de convoyage des boues séchées :
- La vis convoyeuse,
- Les transporteurs tubulaires, à chaine,
- Les transporteurs pneumatiques à phase dense ou à phase diluée,
- Les bandes transporteuses,
- Les élévateurs à godets
Les élévateurs à godets permettent de limiter la dégradation de la structure des boues séchées.
la boucle du fluide caloporteur
La figure 14 représente une boucle de fluide caloporteur type huile thermique et la figure 15 représente le cas d’une boucle avec une seule chaudière pour deux sécheurs en parallèle.

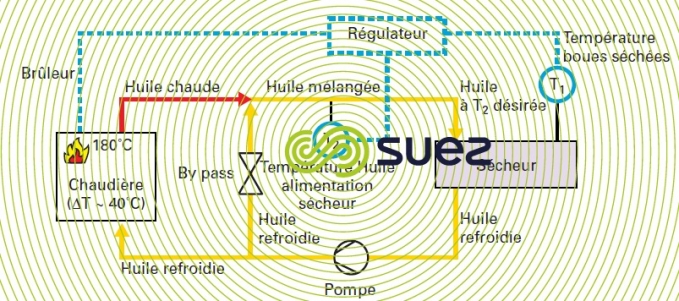


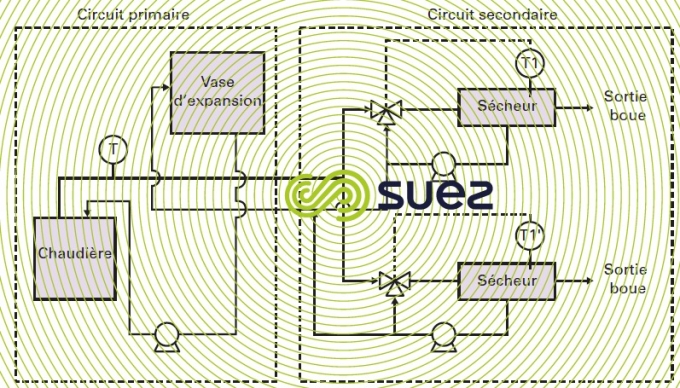

le traitement des buées
La vapeur d’eau générée par le séchage est condensée par refroidissement. Sauf cas particulier d’une plateforme de séchage hors station d’épuration, les condensats sont retournés en tête de station.
Les incondensables sont envoyés pour traitement dans une désodorisation spécifique ou dans celle de la station.
Certains sécheurs, qu’ils soient de type direct ou indirect, disposent de systèmes internes de condensation leur permettant de rejeter des incondensables à faible débit (cas des sécheurs Evaporis™ LE et Evaporis™ LT). Un quench (colonne de condensation) est toutefois fortement recommandé avant la désodorisation.
D’autres technologies de sécheurs comme les sécheurs à tambour (DDS Andritz), les sécheurs à bande, ou les sécheurs mixtes Vomm condensent les buées au travers de condenseurs externes.
La condensation des effluents gazeux est réalisée généralement avec des condenseurs à eau:
- soit par injection directe d'eau froide en grandes quantités (condenseur dit « à contact direct »), c’est le principe d’une colonne de condensation qui fonctionne en circuit ouvert (donc à eau perdue),
- soit dans un condenseur tubulaire dans lequel l'eau circule en circuit fermé et est refroidie dans une tour de refroidissement ou par un groupe froid (condenseur dit « à fluides séparés » ou d’échange indirect). Cette technique permet de renvoyer une quantité d'eau moins importante en tête de station par rapport à un condenseur à contact direct. Dans ce cas, il est possible de valoriser l’énergie disponible en provenance de la chaleur latente de condensation de l’eau évaporée, la boucle d’eau sur le condenseur est fermée au travers d’un échangeur qui produira à son secondaire un réseau de chaleur basse calorie (60-85 °C) (figure 16). La boucle fermée doit comporter une purge de déconcentration à renvoyer en tête.

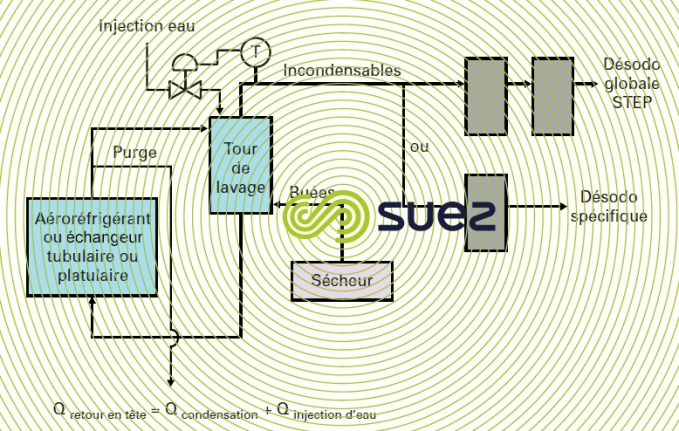

Il existe également des condenseurs à air. C’est le cas par exemple du condenseur présent sur l’Evaporis™ LE entre le 1er étage, sécheur couche mince, et le 2ème étage, sécheur à bande.
Quel que soit le système de condensation mis en place sur les buées d’un sécheur, les incondensables sont extraits et envoyés en désodorisation pour y être traités. Dans le cas de boues non chaulées, séchées sur un sécheur indirect, les buées contiennent des poussières (3 à 5 g·Nm-3) et des produits volatils : COV, NH3, H2S. Les COV sont notamment constitués d’aldéhydes, cétones, amines… Ces composés peuvent justifier la mise en place d’une unité dédiée de désodorisation.
la qualité des condensats
Selon la température des condensats voulue à la sortie du condenseur, le besoin en eau froide pour condenser les effluents gazeux varie de 10 m3 à 30 m3 d'eau par tonne d'eau évaporée pour une colonne de condensation en circuit ouvert. Plus le débit d’eau froide pour la condensation sera important, plus la température des condensats sera basse.
Les condensats de séchage thermique ont donc une température comprise entre 30 et 95 °C. En moyenne leur température est de l’ordre de 60 °C, ce qui signifie que l’on condense au maximum l’eau contenue dans les effluents gazeux extraits du sécheur, mais que l’on n’augmente pas le débit d’eau froide au maximum afin de limiter le débit d’eau à retourner en tête de station.
Dans les stations, la quantité d'eau nécessaire à la condensation des effluents gazeux est facile à obtenir et elle peut être retournée en tête de l'installation de traitement, bien qu'il convienne de prendre en compte la charge de pollution supplémentaire.

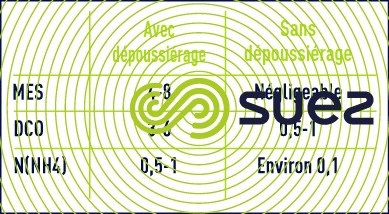

La qualité des condensats est fonction :
- de la nature des boues séchées (boues biologiques, mixtes, digérées),
- du type de sécheur utilisé (temps de séjour et température de fonctionnement) => Plus la température de fonctionnement du sécheur sera faible, moins les buées seront polluées,
- de la qualité de l’eau froide permettant la condensation (eau industrielle en général),
- du débit d’eau froide utilisé pour la condensation.
optionnel : la mise en forme des produits séchés via la pelletisation
Les procédés de séchage ne permettent pas toujours d’obtenir un produit final suffisamment granulé. Ce manque de performance d’auto-granulation est lié au procédé lui-même, mais aussi et surtout à la nature de la boue traitée.
Nos retours d’expérience montrent que :
- une boue exclusivement biologique à haute teneur en MV s’auto-granule aisément ;
- les propriétés d’auto-granulation se dégradent progressivement pour les boues mixtes au fur et à mesure qu’augmente le pourcentage de boues primaires ;
- la digestion affecte peu les propriétés d’auto-granulation ;
- le taux de fibres, principalement dans les boues primaires, dégrade l’auto-granulation. Le taux critique de 5 % est généralement admis (il est défini comme étant le refus sec d’un tamisage humide des boues déshydratées à une maille de 500 µm).
Lorsqu’il n’est pas envisageable de concevoir une unité de séchage sur le principe de l’auto-granulation, il faut avoir recours à un atelier de mise en forme des produits séchés. La technologie la plus répandue est celle dite de pelletisation. Elle consiste à extruder au travers d’une filière le produit préalablement séché. Cette filière a un diamètre compris entre 5 et 8 mm. Le produit extrudé est appelé « pellets » (figure 17).

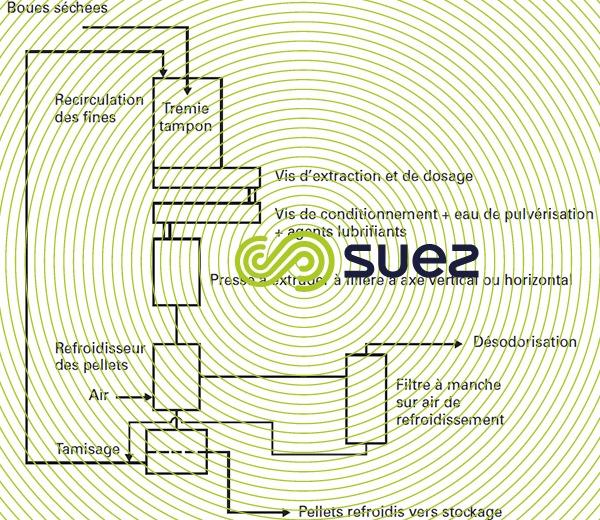

Pour des raisons de sécurité, les pellets doivent être refroidis avant stockage final, courte ou longue durée. Cette température de refroidissement est impérativement inférieure à 40 °C, voire 35 °C (La sécurité des ateliers de séchage).
Les pellets produits sont soumis à des contrôles de qualité :
- granulométrie : il y a généralement des contraintes fortes sur le taux de fines. On entend par « fines » la quantité de produits inférieure à la coupure du tamis correspondant à la taille de la filière. On admet généralement qu’il ne faut pas qu’il y ait plus de 2 % de fines ;
- il y a surtout une contrainte de taux de poussières. Il est à noter que bien des cahiers des charges retiennent un seuil de tamisage de 63 µm avec un taux pondéral ne devant pas excéder 0,1 % de produit passant. Ce niveau nous paraît irréaliste à mesurer et donc à garantir. Nous recommandons de définir comme poussière le passant à 300 µm et que ce taux n’excède pas 1 % ;
- dureté : c’est en fait une résistance à l’écrasement qui est mesurée par une méthode standardisée dite essai Kahl. La résistance à l’écrasement doit être supérieure à 30 N ;
- durabilité (friabilité) : il s’agit d’un test standardisé appelé test de Holmen. Le résultat de ce test doit être supérieur à 90 %.
Si une unité de pelletisation permet d’obtenir des pellets très calibrés et denses (densité de l’ordre de 0,7), les équipements nécessaires au fonctionnement de l’unité de pelletisation sont difficiles à exploiter et induisent des coûts élevés d’exploitation.
L’usure importante des équipements mis en œuvre nécessite un renouvellement fréquent de ces pièces et entraine également une diminution importante de la disponibilité de l’atelier de séchage lors des changements de pièces, mais également en raison des très nombreux arrêts non programmés. Par ailleurs, une unité de pelletisation induit des équipements ATEX comme le refroidisseur des pellets ainsi que le filtre à manche sur l’air de refroidissement en raison de la mise en mouvement des poussières.
Nos retours d’expérience nous amènent à fortement déconseiller la mise en œuvre d’une unité de pelletisation sur les ateliers de séchage thermique.
le stockage des boues séchées
En fonction de l’exutoire final des boues séchées (cimenterie, usine d’incinération des ordures ménagères, compostage, épandage,…), leur durée de stockage peut varier de quelques jours (exemple : cimenterie) à plusieurs mois (exemple : épandage).
Différents types de stockage sont donc possible en fonction de cette durée de stockage, de la place disponible sur place réservée au stockage ainsi qu’en fonction de la forme des boues séchées obtenue :
- Stockage long :
- Casier (pour les moyens à gros volumes)
- Vrac (pour les moyens à gros volumes)
- Big-bag (pour les petits à moyens volumes)
- Stockage court :
- Benne ouverte ou fermée (pour les petits à moyens volumes)
- Silo (pour les moyens à gros volumes)
Quel que soit le type de stockage choisi, la température des boues en entrée de stockeur doit toujours être inférieure à 40°C, voire 35°C avec des boues identifiées « à risque » afin de limiter les risques liés à la problématique d'auto-échauffement des boues.

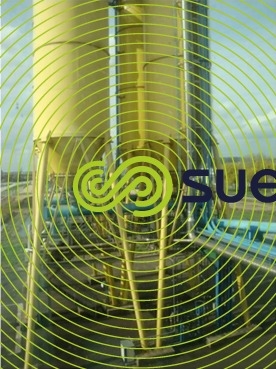


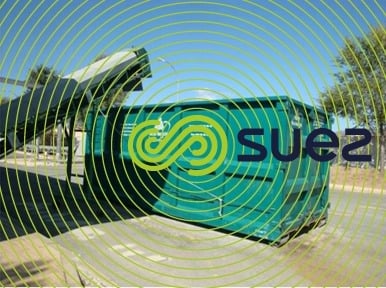


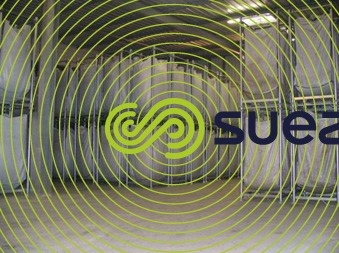


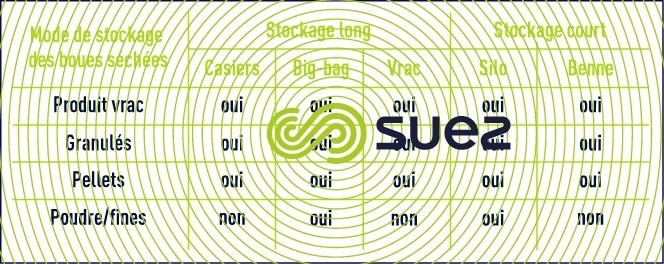

la ventilation de l’atelier de séchage
Un atelier de séchage des boues, composé de nombreux équipements périphériques, doit être suffisamment ventilé afin d’évacuer les calories produites par le sécheur, la chaudière, et les canalisations.
La ventilation permet également de limiter les odeurs dans certaines zones à risque de l’atelier comme la sortie liquide en pied de colonne de condensation, les zones ouvertes, …
Outil Marque-page
Cliquez sur l'outil marque-page, puis surlignez le dernier paragraphe lu pour pouvoir poursuivre ultérieurement votre lecture.
