les types de traitement des fumées
Temps de lecture :Il existe trois grandes familles de procédés : humide, sec ou semi-humide. Autour de ces grandes familles, on peut rencontrer quelques procédés « hybrides ».
le procédé humide
Il est fondé sur la détente iso-enthalpique des fumées pour les amener en présence d’eau à leurs conditions de saturation. Dans ces conditions, les fumées refroidies et saturées vont subir une série de traitements qui vont avoir pour effet de transférer les agents polluants de la phase gazeuse dans la phase liquide. La phase gazeuse épurée pourra être rejetée conformément à la réglementation ; la phase liquide devra être traitée soit de manière spécifique, soit par un retour en tête de station, pour autant que ce retour soit admissible.
Son principe de fonctionnement est basé sur le diagramme de l’air humide (figure 39). Le processus simplifié est le suivant :
- on détermine l’humidité relative de la fumée à traiter, elle est exprimée en g H2O · kg–1 fumées sèches (par exemple 0,35) (point O) ;
- à la verticale de cette valeur, on situe un point A correspondant à la température d’entrée dans le système humide (par exemple 300 °C) et, de ce point, on descend sur la courbe de saturation (φ = 1) suivant une droite parallèle aux iso-enthalpiques (point B) ;
- au croisement avec la courbe φ = 1, on redescend une verticale sur l’axe des abscisses pour déterminer l’humidité à la saturation (point C) ;
- la différence entre la valeur de l’humidité à la saturation et l’humidité relative d’origine donne la quantité d’eau à injecter dans le système par kg de fumées sèches (OC) ;
- à partir du point de saturation (B) sur la courbe φ = 1, on mène une parallèle aux courbes isothermes pour déterminer la température de saturation de ces fumées (point D).
Le processus de saturation décrit s’effectue dans une chambre de saturation (en anglais : quench) dans laquelle on injecte l’eau de saturation avec un léger excès ; le traitement est poursuivi sur deux laveurs (tamis à plateaux ou garnissage) munis chacun d’une boucle de recirculation avec purge de déconcentration et appoint correspondant.
L’intérêt du système humide est que l’on peut y entrer à des températures élevées, par exemple directement après l’échangeur de préchauffage de l’air de fluidisation. Bien évidemment, dans ce cas, il n’y a plus de valorisation ultérieure possible de la chaleur résiduelle des fumées. Ce système est décrit par la figure 40.
Il traite les différentes formes de pollution de la manière suivante :

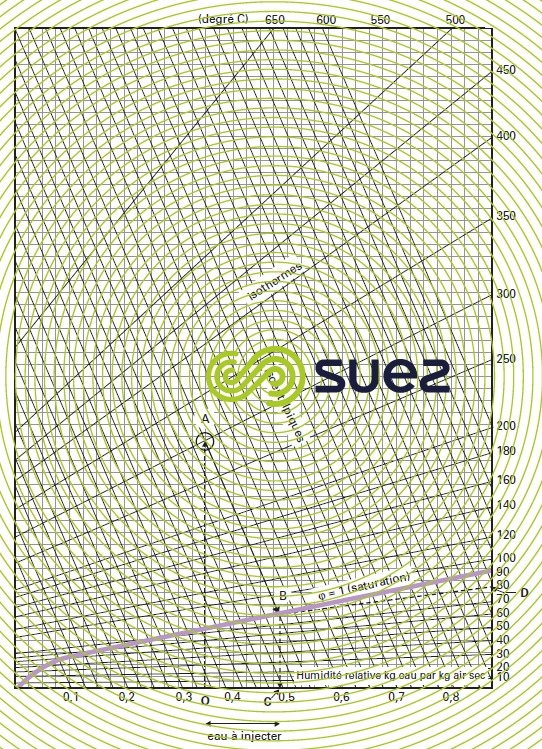


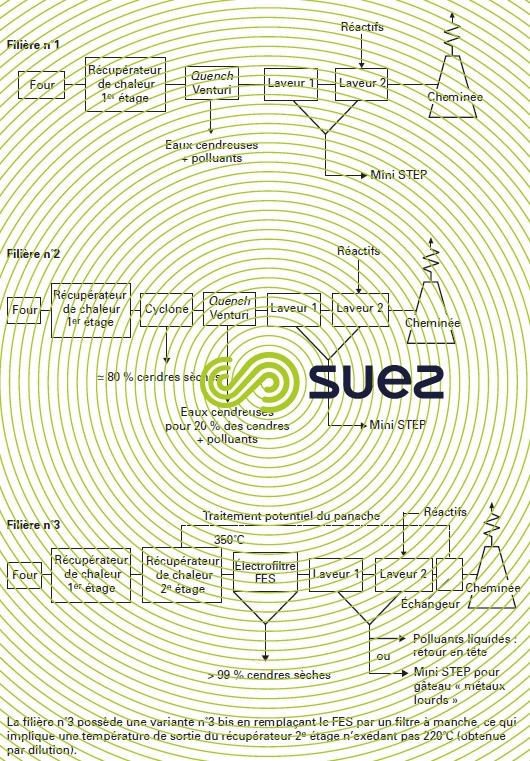

poussières
Elles sont traitées principalement par captation sur les gouttelettes d’eau violemment agitées du fait de la perte de charge du quench venturi. Cette perte de charge doit donc être adaptée à la courbe granulométrique des poussières concernées (la figure 41 définit leur domaine typique). Ceci conduit à un débit d’eau de lavage obtenu par recyclage interne d’environ 10 fois le débit de saturation théorique (représenté par le segment OC dans la figure 39).
Pour l’application en lit fluidisé (teneur moyenne en poussières de 30 g · Nm–3)et compte tenu que le rejet à l’atmosphère, de par la réglementation, ne peut excéder 10 mg · Nm–3, il faudrait que le seul venturi ait un rendement d’abattement supérieur à 99,5 %. Cela ne peut se concevoir qu’avec des pertes de charge supérieures à 100 mbar sinon un traitement complémentaire est nécessaire, soit via un filtre électrostatique humide en finition, soit via un pré-dépoussiérage, soit par cyclone, soit par filtre électrostatique chaud (voir filières 2 et 3 de la figure 40) : cette dernière solution limite également la quantité des eaux « cendreuses » à décanter et à évacuer.
pollution halogènée (Cℓ– et F–)
Cette pollution est aisément éliminée dans le système humide (quench venturi et laveur) grâce à la très grande solubilité des anions Cℓ– et F–. En contrepartie, cela confère à la boucle des eaux de lavage, tournant sur le venturi et le premier laveur, des caractéristiques acides très marquées devant être prises en compte dans le choix des équipements et des matériaux de construction. Cette boucle acide doit éliminer l’essentiel du HgCℓ2 aussi, parfois, le niveau d’acidité doit être régulé par un ajout volontaire d’HCℓ.
pollution soufrée (SO2, SO3)
La pollution soufrée est traitée préférentiellement par un lavage à contre-courant à la soude diluée (laveur 2). La chaux peut être envisagée mais elle présente le désavantage de devoir nécessiter la préparation d’un lait de chaux et de provoquer davantage de problèmes d’entartrage du laveur. Le rendement d’abattement du SO2 dépend de la valeur du pH, celui-ci est donc régulé en fonction de la consigne à l’émission.
pollution métaux lourds volatils
Dans l’hypothèse où l’ensemble quench-venturi-laveurs ne parvient pas à garantir l’émission à 0,05 mg · Nm–3 à cause de la présence de Hg particulaire, le traitement doit être complété :
- soit par l’adjonction d’un filtre électrostatique humide ;
- soit par l’insertion dans le second laveur d’un garnissage spécifique contenant du charbon actif ;
- soit par l’addition d’H2O2 dans le premier laveur.
pollution métaux lourds non volatils
Ils sont fixés par les cendres minérales mais leur fraction lixiviable est solubilisée dans la boucle acide.
pollution dioxines/furannes
Deux solutions sont possibles dans le cas où un traitement spécifique est nécessaire pour garantir l’émission à 0,1 ng · Nm–3 :
- injection de charbon actif en poudre dans la chambre de saturation et adsorption des dioxines (le charbon suit les eaux cendreuses) ;
- insertion d’un étage de garnissage imprégné de charbon actif dans le second laveur.
traitement des purges
Elles ont deux origines :
- l’effluent collectant la charge minérale (poussières) : il est décanté ; le sédiment récupère les cendres minérales humides qui doivent être éliminées en l’état, l’eau surnageante est recirculée dans le process ;
- les deux purges de déconcentration des laveurs doivent être traitées dans une mini-station (problématique similaire mais moins lourde que celle des effluents FGD (voir traitement de l'effluent de désulfuration des fumées des centrales thermiques) avant de pouvoir retourner en tête de station. Ce traitement produit un gâteau de métaux lourds destiné aux centres d’enfouissement techniques de classe 1.
panache
Deux solutions sont envisageables (figure 40) pour le supprimer :
- solution type filière n° 3 consistant à installer un double système d’échangeur amont/aval du traitement humide ;
- solution consistant à implanter un échangeur à tubes de fumées générant de l’air chaud en amont de la chambre de saturation. Cet air chaud est mélangé avec la fumée épurée pour la réchauffer directement et la porter en dehors de la zone de panache.

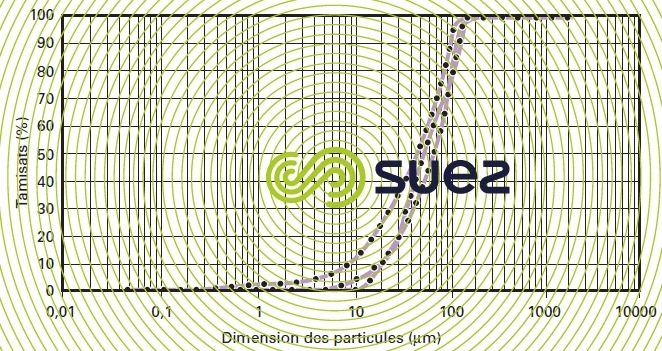

le procédé sec
À l’opposé du traitement humide, le procédé sec traite les fumées telles qu’elles se présentent à la sortie de la valorisation énergétique en faisant le nécessaire pour que la température soit compatible avec les technologies appliquées. Ceci suppose un système contrôlé de refroidissement. Il peut être soit indirect (échangeur), soit direct par addition d’air ambiant ou par pulvérisation d’eau (certaines nomenclatures parlent alors de procédé semi-sec).
Le système est décrit par la figure 42 sous différentes variantes. Il traite les différentes formes de pollution de la manière suivante :
poussières
Elles sont captées principalement par la première étape de dépoussiérage :
- le cyclonage (figure 42 filière 2) (ou multicyclonage) présente l’intérêt de ne pas avoir de contraintes sévères de température ; en revanche, le taux de captation des poussières est très fortement lié à la granulométrie de celles-ci et en fonction de cette granulométrie, le taux d’abattement fluctue entre 50 et 90 % et il est donc à privilégier sur les charges en poussières moins importantes ;
- l’électrofiltre sec et chaud (figure 42 filière 3) (température maximale d’environ 350 °C) ; en fonction du taux d’abattement requis cet électrofiltre peut avoir plusieurs champs en série et son taux d’abattement sera compris entre 98 et 99,5 % ;
- le filtre à manches constitue l’équipement que l’on peut considérer comme le filtre absolu qui permet toujours de garantir un taux d’admission de poussières inférieur à 10 mg · Nm–3. En fonction de la nature des manches, la contrainte de température évolue ; en marche continue, elle est de 220 °C pour des manches à support Téflon.
pollutions halogènées, soufrées, métaux lourds volatils, dioxines
Ces pollutions sont traitées simultanément par des agents neutralisants :
- bicarbonate de sodium ;
- chaux ;
- charbon actif en poudre…
- « sorbalite » (mélange de chaux et d’adsorbant en poudre).
Le bicarbonate et la chaux sont les réactifs de neutralisation de la pollution halogénée et soufrée ; l’adsorbant en poudre adsorbe les métaux lourds volatils, les dioxines et furannes. Compte tenu du principe réactionnel sec et en milieu gazeux avec de faibles temps de séjour, il faut prévoir un excès de réactifs par rapport à la stœchiométrie. Cet excès est différent suivant la nature des réactifs (1,5 pour le bicarbonate ; 3 pour la chaux ; cependant, la réaction avec la chaux est molaire alors qu’il faut 2 moles de bicarbonate pour le même effet de neutralisation).

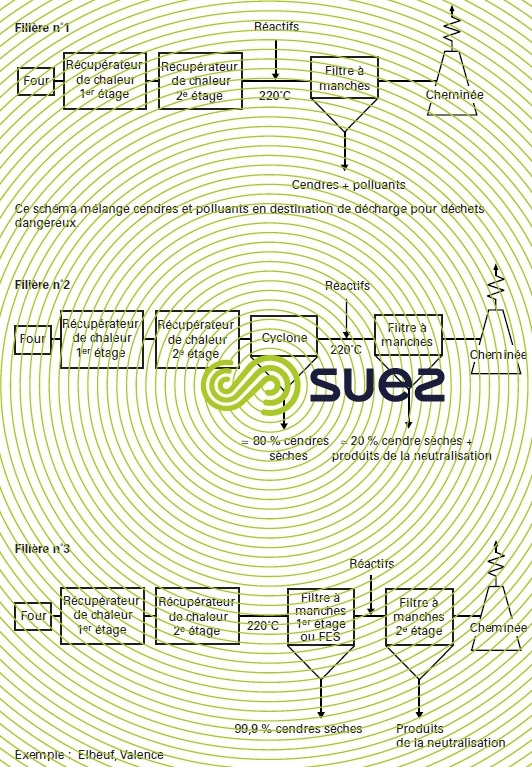

Il faut aussi noter que :
- le bicarbonate de sodium nécessite la mise en place d’une installation de préparation comportant un stockage de produit brut et un concassage afin qu’il ait la réactivité requise ;
- compte tenu du coût de la mise en décharge des résidus finaux, il peut dans certains cas être opportun de doter l’installation d’un traitement des gâteaux de neutralisation consistant à redissoudre le bicarbonate. La fraction aqueuse est recyclée en tête et il ne subsiste qu’un résidu final constitué essentiellement de l’adsorbant chargé des métaux lourds.
panache
C’est un des intérêts du procédé sec, il n’y a pas d’apparition de panache (à l’exception éventuelle de conditions d’hygrométrie très faible et de température largement inférieure à 0 °C).
La photo 19 présente l’installation d’Elbeuf comportant un four à lit fluidisé de diamètre de 2,3 m (1), les échangeurs de chaleur (2) et deux filtres à manche en série (3).

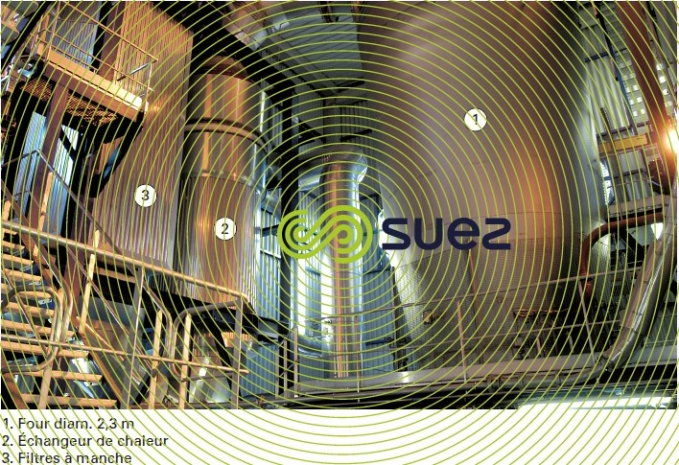

le système semi-humide
Il s’agit en fait de système hybride entre les systèmes humide et sec tentant de conserver les avantages et de limiter les inconvénients de chacun des systèmes.
Le système humide a deux inconvénients majeurs :
- la production d’eaux cendreuses particulièrement pénalisante quand la charge en poussières est très élevée (lit fluidisé) ;
- la nécessité d’un traitement des purges provenant des différentes étapes de lavage.
Le système sec a deux inconvénients majeurs :
- il faut refroidir les fumées avant de rentrer dans la chaîne de traitement ; ce conditionnement est particulièrement strict lorsqu’il s’agit de filtres à manches ;
- la surstœchiométrie réactionnelle propre au système sec qui représente un coût d’exploitation significatif.
Pour compenser ces désavantages, le procédé (figure 43) semi-humide correspond en fait à un procédé humide mais à purge nulle.
Il consiste donc à faire précéder le traitement humide (laveurs) d’une tour de réaction dans laquelle on pulvérise et évapore les purges. Ce système n’est possible que si la chaleur sensible contenue dans les fumées permet de compenser l’évaporation et la surchauffe de l’eau contenue dans ces purges. Les sels de cristallisation sont récupérés en bas de cette tour ou dans le filtre à manche. Ce principe ne peut convenir qu’aux fumées peu chargées en poussières, il s’applique donc bien aux procédés de pyrolyse (dans ce cas, il est très économique tant en investissement qu’en frais de réactifs) mais difficilement aux procédés d’incinération de type lit fluidisé.
Pour rendre ce système compatible avec de fortes charges en poussières, il faut faire précéder la tour d’un pré-dépoussiérage (par ex. électrofiltre chaud) – voir filières 1 et 2 (figure 43).

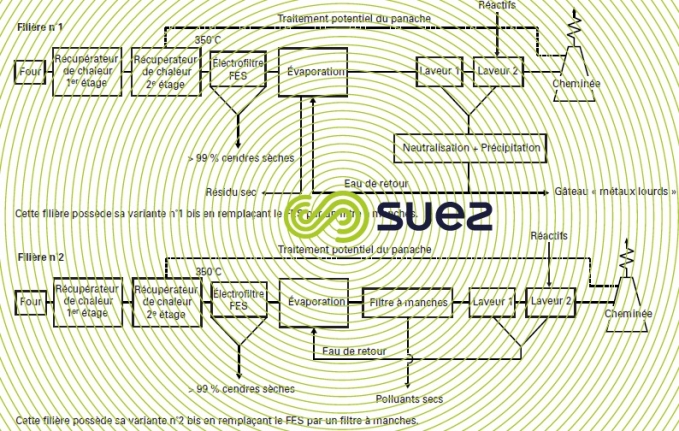

le traitement de la pollution oxyde d’azote (NOx)
Quelles que soient les filières décrites ci-dessus, elles n’éliminent pas la pollution liée aux oxydes d’azote (NOx). Pour ce faire, tous les procédés font réagir une solution ammoniacale avec les NOx suivant la réaction globale :


Cette réaction est catalysée de deux manières :
- soit à haute température (900 °C environ) : catalyse homogène appelée SNCR ;
- soit à basse température (200-300 °C) catalyse hétérogène appelée SCR (catalyseur sur support nids d’abeilles traversés par la fumée).
La voie SNCR, lorsque le procédé thermique le permet, est simple à mettre en œuvre. Il suffit d’injecter une solution ammoniacale ou un sel d’urée dans la zone du process où la température des fumées voisine 900 °C. Dans le procédé humide, l’éventuel excès de NH3 se trouve automatiquement neutralisé. Dans le système sec, il suppose l’insertion d’un laveur en aval du filtre à manches ce qui fait perdre en partie les avantages spécifiques liés à ce procédé (ex. absence de panache…).
Dans le cas de l’incinération dédiée en four à lit fluidisé, il est courant de respecter le niveau d’émission de 200 mg · m–3 sans avoir recours à une dé-NOx spécifique. Lorsque la nature des boues ou les conditions opératoires ne permettent pas de respecter cette contrainte, les retours d’expérience montrent que l’on peut raisonnablement tabler sur un abattement de 50 % des teneurs en NOx. Si un abattement de 50 % est insuffisant pour atteindre les seuils réglementaires, une solution SCR doit s’appliquer.
La solution SCR est beaucoup plus complexe à implanter. Elle doit l’être en aval du traitement des fumées car la durée de vie des catalyseurs est fortement compromise s’ils sont en contact avec les impuretés (essentiellement SO3) des fumées non purifiées. Appliquée à un traitement humide ou semi-humide, l’installation d’une SCR nécessite :
- l’implantation d’un réseau d’échangeurs huile thermique destiné à prélever l’énergie contenue dans les fumées en amont pour la restituer en aval pour le préchauffage à la température requise par la SCR (en revanche, pour le traitement sec, ce système n’est pas requis) ;
- une perte de charge élevée nécessitant la mise en place d’un second ventilateur d’extraction ;
- un brûleur d’appoint pour contrôler rigoureusement la température réactionnelle ;
- comme pour la SNCR, un stockage de solution ammoniacale ou de sel d’urée.
La figure 44 montre une réalisation de SCR jumelées avec un traitement sec.

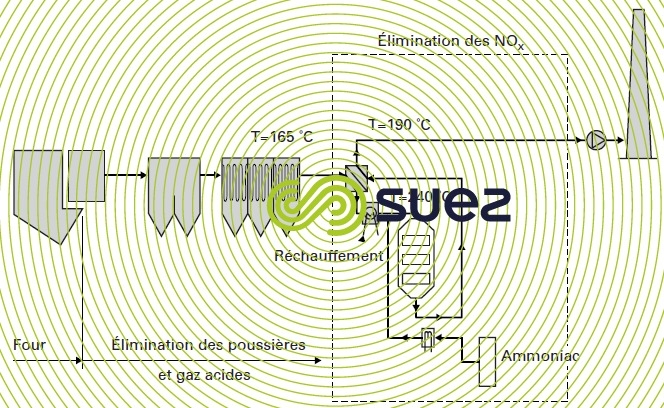

Outil Marque-page
Cliquez sur l'outil marque-page, puis surlignez le dernier paragraphe lu pour pouvoir poursuivre ultérieurement votre lecture.
