filtre-presse classique à plateaux chambrés
Temps de lecture :La filtration s’effectue sous pression en chambres étanches. Contrairement au filtre à bandes, la boue est obligée de subir la contrainte appliquée (pas de fluage possible).
Cette technique, relativement ancienne, reste très répandue. Son atout majeur, et très souvent décisionnel, est la production d’un gâteau qualifié « solide », généralement à plus de 30 % MS (donc la gamme de siccité la plus élevée en déshydratation mécanique). Pourtant, ses désavantages restent majeurs :
- caractère discontinu du fonctionnement (bâchées successives appelées cycles) ;
- débit d’alimentation dégressif tout au long du cycle ;
- investissement plus élevé que les autres ateliers de déshydratation mécanique ;
- décharge mécanisée entre chaque cycle mais aide manuelle généralement inévitable pour la tombée des gâteaux (tout au moins avec une grande majorité de boues).
À noter cependant quelques voies de progrès ces dernières années :
- fiabilisation d’un conditionnement aux polymères donc sans utilisation de chaux ;
- quelques filtres automatiques ont été développés mais la sûreté mécanique et la fiabilité opérationnelle restent à confirmer sur l’ensemble des boues notamment les boues hydrophiles difficiles.
description générale d’un filtre-presse classique (figure 40)

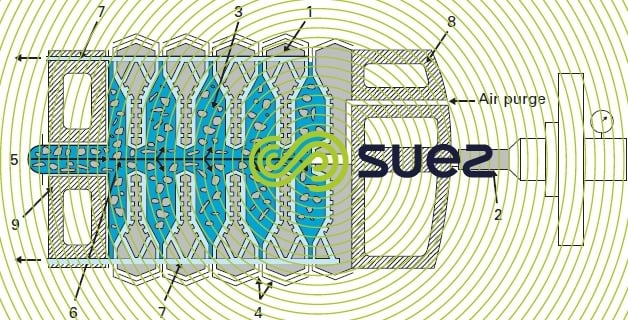

Un filtre est constitué par une batterie de plaques évidées (1), verticales, juxtaposées et serrées fortement les unes contre les autres par une tête mobile (8) actionnée par un(des) vérin(s) hydraulique(s) (2) placé(s) à une des extrémités de la batterie. La poussée de l’ensemble tête mobile/plaques est contenue par une tête fixe (9), placée à l’autre extrémité.
Cette disposition en plaques verticales formant des chambres de filtration étanches (3) permet une mécanisation aisée pour la décharge des gâteaux (« débâtissage »).
Sur les deux faces cannelées des plaques, sont placées des toiles filtrantes (4) de mailles assez serrées (10 à 300 mm).
Les boues à filtrer (5) arrivent, par pompage, dans les chambres de filtration par l’intermédiaire d’orifices (6) aménagés généralement au centre des plateaux : l’alignement de ces orifices constitue le conduit d’alimentation en boue.
Les matières solides s’accumulent progressivement dans la chambre de filtration jusqu’à formation d’un gâteau final compacté.
Le filtrat est recueilli dans les cannelures du plateau, à l’arrière des toiles filtrantes et évacué au moyen de conduits internes (7) (donc sans nuisances extérieures).
La pression engendrée par le(s) vérin(s) de serrage doit être calculée pour que la pression d’étanchéité appliquée sur les plans de joint de chaque plateau filtrant soit supérieure à la pression interne de la chambre développée par le système de pompage de la boue.
technologies de mise en œuvre
Elles se différencient essentiellement par :
- le supportage des plaques filtrantes : soit latéral sur deux barres longitudinales (photo 22), soit par accrochage à un ou deux rails supérieurs (photo 23) ;

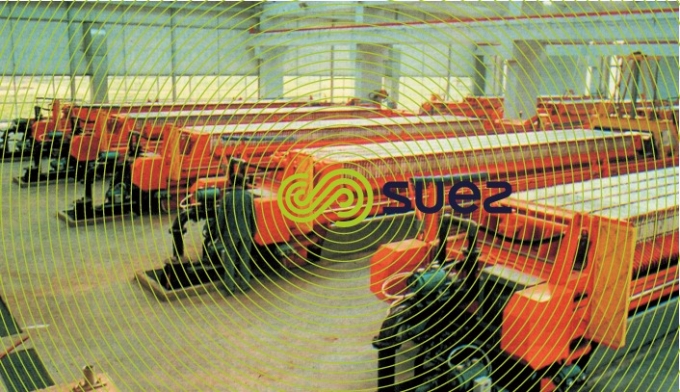


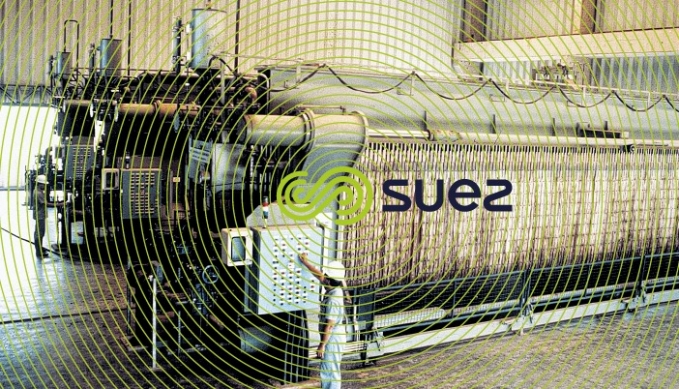

- le système de halage des plaques, une à une (électromécanique ou hydro-mécanique) (photo 24) ;

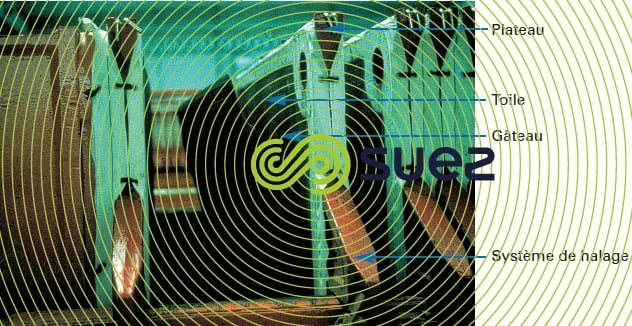

- le système de serrage : un ou plusieurs vérins hydrauliques ;
- le système de lavage haute pression des toiles. Il faut des pressions de 80-100 bar pour laver les toiles et les cannelures avec des rampes de lavage pas trop éloignées des toiles pour que la pression soit efficace ;
- les coefficients de sécurité adoptés dans le calcul du bâti support ;
- la taille des appareils : des petits filtres (20 à 30 plateaux de 500 × 500) aux plus grands (150 à 160 plateaux de 2 000 × 2 000 soit des volumes globaux de 15 000 à 18 000 litres et plus de 1 000 m2 de surface de filtration pour une surface au sol de l’ordre de 40 m2, donc assez compact) ;
- les pressions appliquées : 15 bar en standard mais pour certaines boues des versions 7 bar (moins chères) sont disponibles chez certains fournisseurs ;
- l’épaisseur des gâteaux : la profondeur des chambres, donc l’épaisseur finale du gâteau est choisie en fonction de la nature de la boue. Pour des boues denses de très bonne filtrabilité, des fortes épaisseurs (50 mm) évitent d’avoir des cycles trop courts, pénalisants. Pour la majorité des boues urbaines, l’épaisseur préconisée est 30 mm, bon compromis entre temps de cycle et poids du gâteau ;
- la technologie des plateaux : le matériau polypropylène est maintenant généralisé (on trouve encore des plateaux fonte pour les plus grandes unités). Chaque plateau comporte un certain nombre de bossages, uniformément répartis. Ces bossages évitent les déformations de la partie interne des plaques filtrantes en cas de mauvais remplissage du filtre-presse ;
- les toiles filtrantes : dans la majorité des applications, ce sont des toiles tissées en fibres synthétiques, mono-filament (polypropylène ou polyamide-rilsan). La toile est le plus souvent montée sur une sous-toile plus grossière (meilleure évacuation des filtrats et moins de contraintes pour la toile fine de filtration).
Pour des boues d’hydroxydes à flocs très fins, on met en place des toiles multifilaments, plus fermées.
Dans un atelier bien entretenu, la durée d’utilisation des toiles est supérieure à 2000 cycles.
cycle de filtration
Le filtre-presse opère par pressées successives. Chaque pressée comprend les différentes phases suivantes :
- fermeture de la presse : le filtre étant complètement vide, la tête mobile, actionnée par le(s) vérin(s), serre les plateaux entre eux. La pression de fermeture est autorégulée pendant toute la filtration de façon à ce que l’étanchéité soit assurée au niveau des plans de joint ;
- remplissage du filtre : cette phase est de courte durée (10 min maxi). Les chambres de filtration sont remplies de boues à filtrer par l’intermédiaire de la pompe d’alimentation. Le temps de remplissage choisi dépend de la filtrabilité de la boue (d’autant plus court que la filtrabilité est bonne) ;
- filtration : une fois les chambres remplies, l’arrivée continue de la boue provoque une montée en pression, par suite de la formation d’une couche de boue filtrée, de plus en plus épaisse, sur les toiles filtrantes. La pression maximale de filtration est souvent atteinte en 30-45 min. Les durées de filtration peuvent varier de 1 à 5 h selon la profondeur des chambres et la filtrabilité. La phase de filtration est arrêtée généralement par minuterie (temps programmé de maintien à la pression maximale) de façon à obtenir un débit final de filtrat de 5 à 10 L · m–2 de surface filtrante et par heure en conditionnement par polymère et 10 à 20 L · m–2 · h–1 en conditionnement minéral. Lorsque la pompe de filtration est arrêtée, les circuits internes de boue et filtrat sont vidés à l’aide d’air comprimé ;
- débâtissage : la tête mobile est reculée pour ouvrir la première chambre de filtration. Le gâteau formé tombe de son propre poids. Par un système mécanisé, les plateaux sont alors tirés un à un. Selon le degré de collage du gâteau sur les toiles, la durée de débâtissage se situe entre 15 et 45 min pour un filtre équipé d’une centaine de chambres. Cette phase réclame la présence d’un surveillant car beaucoup de boues, avec un taux de conditionnement minimal ou un conditionnement par polymère, fournissent des gâteaux plus ou moins collants et il faut alors intervenir avec un racloir pour assurer leur évacuation complète.
À ces quatre phases du cycle de filtration, il faut ajouter la phase très importante denettoyage : nettoyage de la toile et des rainures d’évacuation du filtrat. Ce lavage s’effectue tous les 10-15 cycles pour un conditionnement aux polymères ou tous les 30-40 cycles pour un conditionnement minéral. Les laveurs (photo 25) fonctionnent sans présence de personnel sur les grosses unités. Ils sont synchronisés avec le halage des plateaux. La durée d’un lavage est d’environ 2-3 heures. En cas de conditionnement massif à la chaux, il est nécessaire (tous les 500 cycles environ) de procéder à un détartrage des toiles et plateaux : généralement par trempage ou circulation d’une solution HCℓ passivé, titrant 5-7 %.
Le filtre-presse consomme relativement peu d’énergie : de l’ordre de 25 à 35 kWh · t–1MES selon les types de boues.

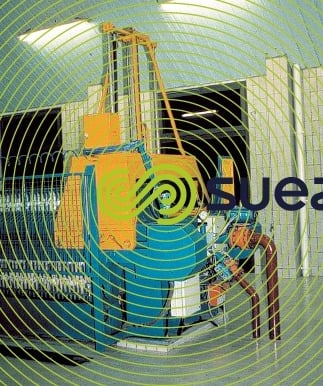

dimensionnement d’un filtre-presse
Il faut connaître :
- la quantité de MES (boues + réactifs de conditionnement additionnés) à filtrer par jour ouvré = M ;
- le temps de cycle global = T (dépend de l’épaisseur du gâteau et de la résistance spécifique r0,5 de la boue conditionnée) ; le temps de cycle T permet de décider du nombre K de cycles possibles par jour de travail (selon le temps d’exploitation) ;
- la siccité moyenne finale du gâteau de filtration SF ;
- la densité d du gâteau
Un filtre-presse est dimensionné par le volume VT total des chambres de filtration :

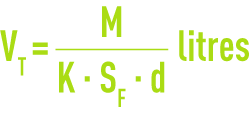
avec :
M en kg MES · j–1
SF en fraction (= 100 SF en %/ MS).
Un compromis économique est alors à faire entre le nombre de gâteaux et la gamme de dimensions des plateaux.
À noter que le filtre-presse est l’appareil de déshydratation mécanique donnant les meilleurs rendements de séparation (de l’ordre de 98-99 %).
performances avec conditionnement minéral
Le tableau 22 donne un aperçu des performances obtenues avec quelques boues hydrophobes (pas de conditionnement), quelques boues hydrophiles de tendance minérale (conditionnement par simple chaulage) et quelques boues hydrophiles de tendance organique (double conditionnement par sel ferrique et chaulage).



La figure 41 schématise l’atelier de filtration correspondant à cette dernière application.

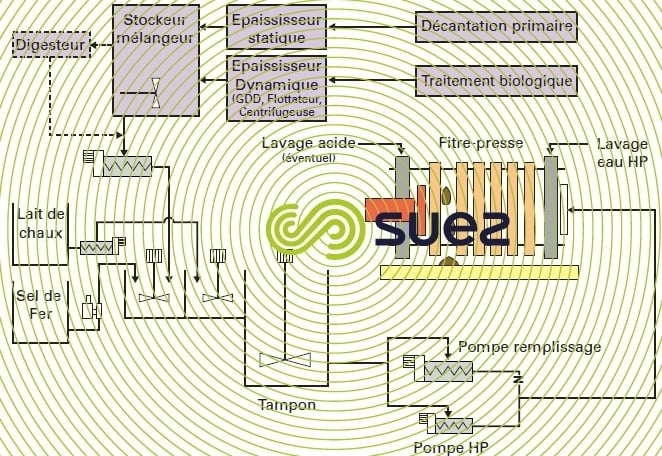

performances avec conditionnement polymère
Le conditionnement par polymère est attractif car il n’y a pas d’augmentation du tonnage de déchets (ce qui n’est pas le cas avec le conditionnement minéral où souvent des doses importantes de chaux sont ajoutées). En revanche, sur une grande majorité de boues, le gâteau produit est plus ou moins collant ce qui augmente le temps de débâtissage et les interventions manuelles à la chute du gâteau.
Le chlorure ferrique doit être couplé au polymère sur les boues organiques de façon à réduire ces collages.
Du fait du non apport de charge minérale, les siccités obtenues sont bien sûr plus faibles et les gâteaux de structure plus spongieuse.
Le tableau 23 donne quelques performances sur des boues résiduaires urbaines.
Les figures 42, 43, et 44 donnent plusieurs exemples de mise en œuvre d’un conditionnement polymère dans un atelier filtre-presse.

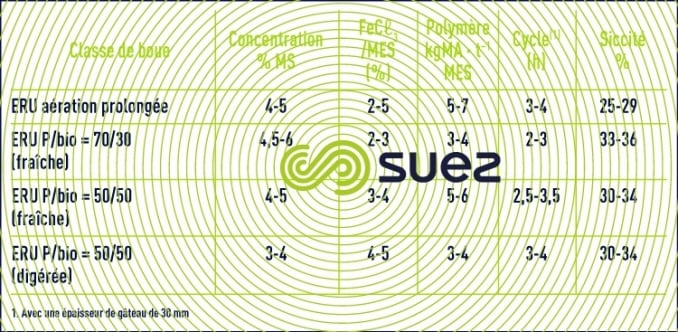

Les installations avec conditionnement mixte (minéral avec chaux ou polymère – figure 43) sont très intéressantes : en effet, le conditionnement par chaulage permet de répondre aux besoins de la filière agricole pour l’évacuation finale. Si cette filière devient impossible ou difficile un conditionnement par polymère permet alors l’envoi vers un séchage thermique ou en incinération et ceci en gardant des siccités acceptables et donc un PCI maximal.

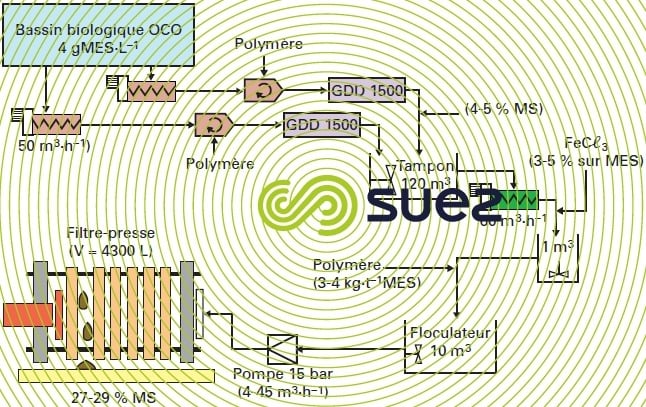


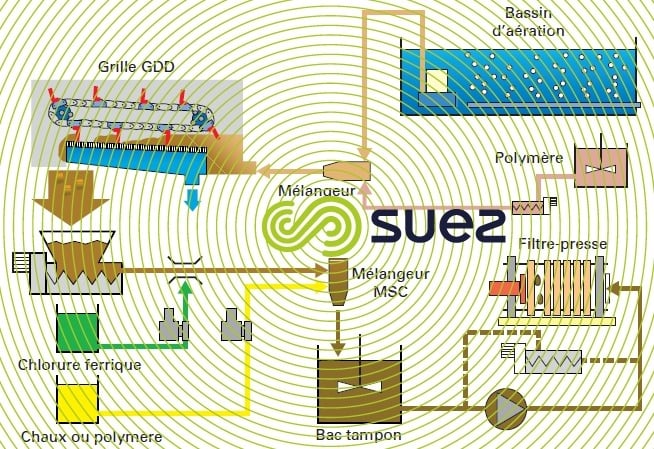


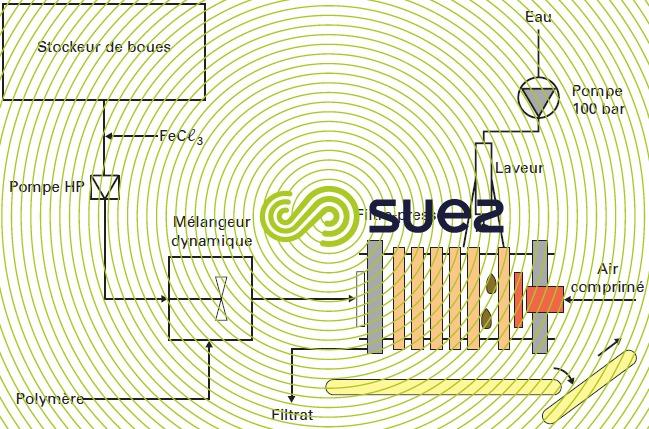

Outil Marque-page
Cliquez sur l'outil marque-page, puis surlignez le dernier paragraphe lu pour pouvoir poursuivre ultérieurement votre lecture.
